Schweißverfahren Übersicht
Das Schweißen hat einen langen Entwicklungsweg hinter sich und da überrascht es auch nicht, dass es sich in verschiedene Richtungen bewegt hat. Daraus sind eine ganze Reihe von verschiedenen Schweißmethoden entstanden, denen wir uns in diesem Kapitel in Form einer Schweißverfahren Übersicht einmal mehr widmen wollen
Inhaltsverzeichnis
- Schweißverfahren Übersicht
- Was ist Feuerschweißen?
- Wie funktioniert Schmelzschweißen?
- Was macht man beim Verbindungs-, Auftrags- und Bahnschweißen?
- Wie funktioniert Metallschutzgasschweißen (MSG)?
- Was ist Wolfram-Inertgasschweißen (WIG)?
- Was bedeutet Plasmaschweißen?
- Wie funktioniert Arcatom-Schweißen?
- Was ist wichtig beim Punktschweißen?
- Was ist Rollennahtschweißen?
- Was versteht man unter Buckelschweißen?
- Wie funktioniert Unterpulverschweißen?
- Was ist Laserstrahlschweißen?
- Wie geht Elektronenstrahlschweißen?
- Was versteht man unter Thermit-Schweiß en ?
- Was bedeutet Kaltpressschweißen?
- Wie geht Reibschweißen?
- Was ist Rotationsreibschweißen?
- Wie funktioniert Reib rührschweißen ?
- Was ist LAFSW-Schweißen?
- Wie geht Ultraschallschweißen?
- Was ist Sprengschweißen?
- Was versteht man unter Diffusionsschweißen ?
Geschätzte Lesedauer: 21 Minuten
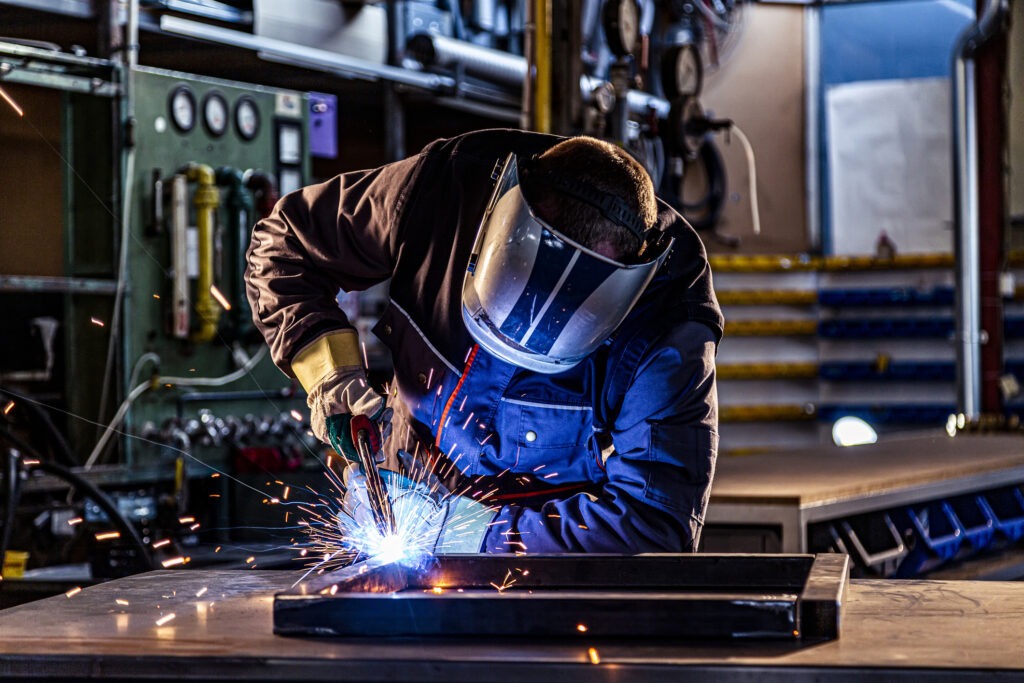

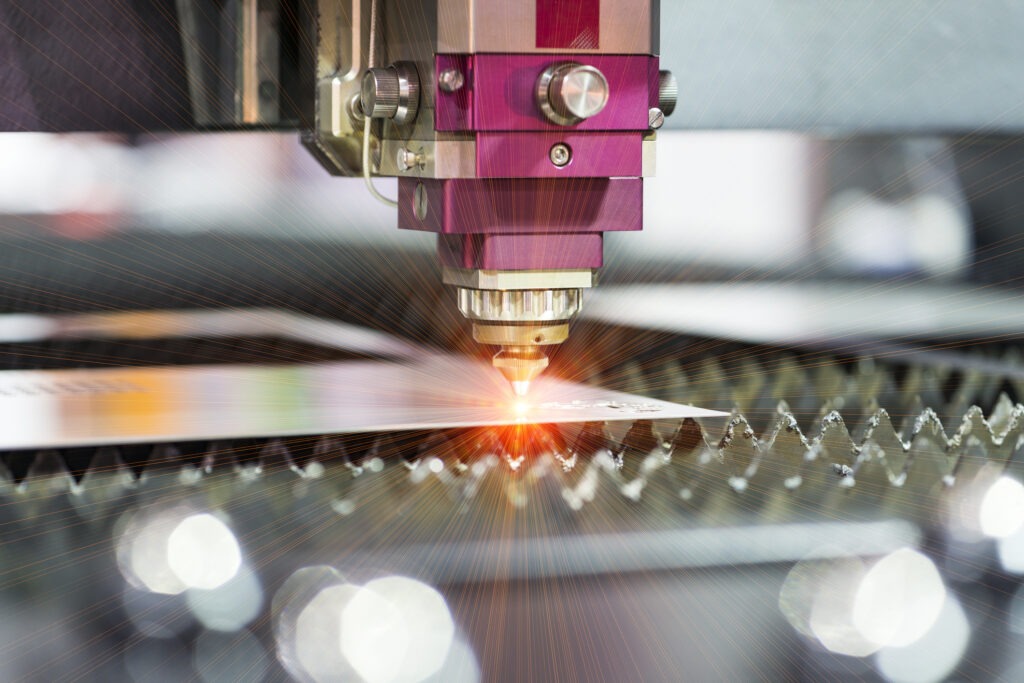
Was ist Feuerschweißen?
Die älteste noch heute bekannte Methode des Schweißens ist das Feuerschweißen. Hier werden im Feuer unter dem Abschluss von Außenluft die Metalle, die verbunden werden sollen, in einen Zustand gebracht, der sich als teigig beschreiben lässt. Unter Druck wurden diese Teile dann verbunden. Der Druck wurde zum Beispiel mit Hammerschlägen erzeugt. Dabei kommt es darauf an, stark genug zu sein, um einen ausreichenden Druck aufzubauen, aber nicht zu stark, um die Teile nicht sofort wieder auseinander zu prellen.
Die Temperaturen liegen beim Feuerschweißen bei 1200 bis 1300 °C an der Oberfläche der Materialien. Der Stahl wird dabei nicht aufgeschmolzen. Damit er jedoch nicht oxidiert, muss dabei ein Eindringen von Luft verhindert werden. Dies geschah am Anfang durch den Einsatz eines feinkörnigen Flusssandes. Dieser erreichte zwar einen guten Luftabschluss, doch er machte es auch schwierig, den richtigen Schmelzpunkt zu erreichen. Heute kommt dafür Borax zum Einsatz. Daraus entsteht eine flüssige Haut, die sich über die Stahlteile ausbreitet und diese damit vor dem Eindringen von Luft bewahrt.
Das Feuerschweißen kam bei Schmieden zur Herstellung von Waffen zum Einsatz. Damit wurden zum Beispiel Schwerter und Dolche hergestellt, die aus dem sogenannten Damaszener Stahl bestanden.
Wie funktioniert Schmelzschweißen?
Beim Schmelzschweißen wird ein Schmelzfluss erzeugt, ohne dass dabei Kraft zum Einsatz kommt. Es können jedoch Schweißzusätze verwendet werden. Es ist wichtig, dass nach dem Schweißen die Werkstoffe nach dem Abkühlen über die gleichen Eigenschaften verfügen, wie es vor dem Erhitzen der Fall war.
Das Schmelzschweißen wird zwar meistens für metallische Materialien verwendet, es kann aber auch bei anderen Werkstoffen eingesetzt werden. Dazu zählen zum Beispiel Glas und Glasfasern, sowie thermoplastische Kunststoffe. Auch hier können Schweißnähte angelegt werden. Es lassen sich aber auch mit Schweißpunkte und Schweißflächen, wie beim Reibverschweißen, arbeiten.
Wird das Schmelzschweißen für Stahl angewendet, ist zu beachten, dass sich damit nur einfache Stähle bis zu einem Kohlenstoffgehalt von 0,22% C und einer Festigkeit von 500 N/mm2 dauerhaft verbinden lassen. Stähle die legiert sind oder eine höhere Festigkeit aufweisen, benötigen weitere Maßnahmen, um eine Bildung von Brüchen und Rissen zu vermeiden.
Zu den weiteren Maßnahmen gehören das Vorwärmen, ein langsames Abkühlen, ein Anlassen oder ein Spannungsarmglühen. Auch können spezielle Schweißverfahren genutzt werden.
Was macht man beim Verbindungs-, Auftrags- und Bahnschweißen?
Das Verbindungsschweißen dient dazu, zwei Werkstücke zu verfügen. Das ist zum Beispiel bei einer Rohrlängsnaht der Fall. Das Auftragsschweißen dagegen ist das Beschichten eines Werkstückes im Schweißverfahren. Dabei sind die Werkstoffe für das Werkstück und das Auftragen verschieden. Diese Form des Schweißens kommt vor allem bei Panzerungen, Pufferschichten und Plattierungen zum Einsatz.
Das Bahnschweißen erfolgt mit Hilfe von Robotern. Diese verschweißen Werkstoffe automatisch ohne weiteres menschliches Zutun.
Wie funktioniert Metallschutzgasschweißen (MSG)?
Das Metallschutzgasschweißen, kurz MSG, unter das die MIG und MAG fallen, ist ein noch jüngeres Lichtbogenschweißverfahren. Es wurde in den USA in 1948 entwickelt und schaffte es kurz danach, Europa zu erreichen.
Am Anfang kamen dabei inerte Gase oder Argon zum Einsatz. Diese enthielten nur geringe Mengen an Sauerstoff und anderen aktiven Bestandteilen. Daher hieß das Verfahren zuerst SIGMA-Schweißen. Sigma stand für „shielded inert gas metal arc“.
Inertgase waren jedoch teuer und die Sowjetunion wollte die damit verbunden Kosten nicht tragen. Daher wurden dort ab 1953 auch aktive Gase, zum Beispiel Kohlendioxid, eingesetzt. Das wurde dadurch möglich, dass neue Drahtelektroden entwickelt wurden. Diese Elektroden trugen dem Umstand Rechnung, dass mit aktiven Gasen die Elemente der Legierungen stärker abbrannten.
Der Schweißdraht schmilzt im Laufe der Schweißarbeiten ab. Um diesen nicht zu erschöpfen, wird durch einen Motor der Draht kontinuierlich nachgeführt. Die Geschwindigkeit des Motors lässt sich dabei einstellen.
Was ist Wolfram-Inertgasschweißen (WIG)?
Das Wolfram-Inertgasschweißen wird im Deutschen mit WIG abgekürzt. Im Englischen dagegen findet sich die Abkürzung TIG von dem englischen Wort Tungsten für Wolfram. In den USA wurde das Verfahren 1936 al Argonarc-Schweißen eingeführt. Nach dem 2. Weltkrieg verbreitete es sich auch in Deutschland.
Das WIG-Impulsschweißen
Aus dem WIG-Verfahren entstand auch das WIG-Impulsschweißen. Hier wird pulsierender Strom eingesetzt, der es erlaubt, die Wärmeeinbringung in das Werkstück sehr fein zu dosieren. Das macht eine Spaltüberbrückung sehr einfach. Auch wird damit eine gute Wurzelschweißung möglich und das Schweißen in Zwangslagen erleichtert. Gerade Schweißnahtfehler, die am Anfang oder Ende einer Naht gern auftreten, werden damit ebenfalls vermieden.
Das WIG-Orbitalschweißen
Das Orbitalschweißen ist ein Schweißen, bei der eine Verbindung mit mindestens einem Rundkörper hergestellt wird. Dabei handelt es sich in den meisten Fällen um ein Rohr. Dafür wird der Lichtbogen um den Rundkörper, der fixiert ist, geführt. Gewöhnlich führt der Lichtbogen dabei mindestens eine volle Umdrehung ohne Unterbrechung, also 360°, aus.
Das Verfahren gehört zu der Gruppe des teilmechanisierten Schweißens. Dabei wird die WIG-Methode verwendet, weil sie es erlaubt, das Schmelzbad sehr gut unter Kontrolle zu halten. Damit gelten für das WIG-Orbitalschweißen die gleichen Regeln hinsichtlich der Sauberkeit und Verschweißbarkeit der verwendeten Werkstoffe, wie mit allen anderen WIG-Schweißverfahren.
Das Orbitalschweißen ist darüber hinaus auch immer dann von Bedeutung, wenn die Ansprüche hinsichtlich der Qualität der Schweißnaht besonders hoch sind. Dabei geht es nicht nur um die Festigkeit, sondern auch die Röntgensicherheit und die Ausbildungsform der Naht. Hier geht es für viele Nutzer vor allem um eine geringe Rauheit gepaart mit einer gleichmäßigen und vor allem flachen Wurzel. Daraus ergeben sich auch die Anwendungsbereiche, die von der Pharmazie bis hin zur Lebensmittel- und Biotechnik reichen.
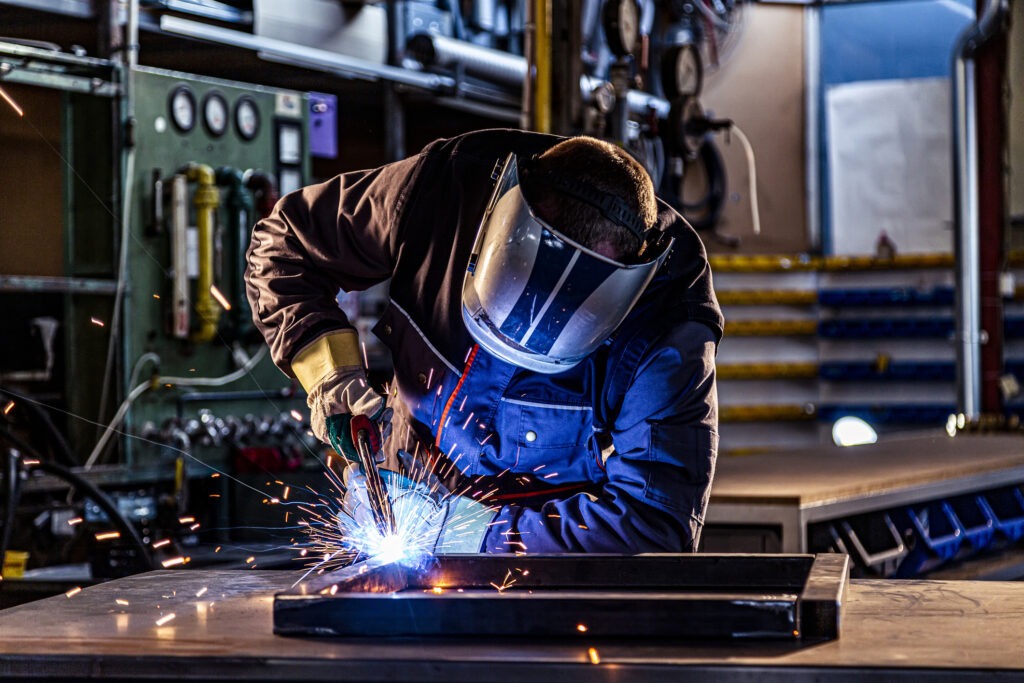
Was bedeutet Plasmaschweißen?
Das Plasmaschweißen verwendet einen Plasmastrahl als die Wärmequelle, mit der der Werkstoff geschmolzen wird. Das Plasma selbst wiederum ist ein Gas, das elektrisch leitend ist und mittels eines Lichtbogens hocherhitzt wird.
Im Plasmabrenner wird Argon als Plasmagas eingesetzt. Dieses wir über Hochfrequenzimpulse ionisiert und mit einem Pilotlichtbogen gezündet. Die Elektrode besteht aus Wolfram und ist negativ gepolt. Das Werkstück ist positiv gepolt. Zwischen beiden entsteht über eine Düse eine Gassäul, welche dabei ionisiert wird. Das erlaubt das Zünden des Lichtbogens ohne eine Berührung.
Der Plasmastrahl, der den übertragenen Lichtbogen bildet, ist selbst von einem Mantel aus einem Schutzgas umgeben. Dabei kommt zum Beispiel Argon zum Einsatz, welches 5% bis 7% Wasserstoff enthält. Das Schutzgas hilft auch hier, den Lichtbogen zu stabilisieren und es schützt das Schmelzbad vor der Oxidation mit dem Sauerstoff in der Luft.
Der Plasmalichtbogen, der durch die Gassäule entsteht, wird durch die verwendete Kupferdüse eingeengt. Diese Düse wird permanent mit Wasser gekühlt, um sie vor der Hitze zu schützen. Die Gassäule hat eine fast perfekte zylindrische Form. Das erlaubt es, die verwendete Energie auf den Punkt des Schweißens zu konzentrieren. Damit ist es möglich, das Schmelzen zu beschleunigen, was insgesamt zu einer höheren Schweißgeschwindigkeit führt. Auch ist der Verzug des Werkstückes dadurch geringer und es kommt zu weniger Spannungen.
Die verwendeten Stromstärken können sehr gering sein und noch unterhalb von 1 Ampere brennt der Plasmalichtbogen stabil. Auch ist er gegenüber einer Veränderung seiner Länge unempfindlich. Das heißt, der Abstand der Düse zum Werkstück hat einen geringen Einfluss, was auch den Einsatz im Mikroschweißen ermöglicht. Damit lassen sich sogar Bleche mit einer Stärke von nur 0,1 mm schweißen. Daraus ergeben sich dann auch die Hauptanwendungsgebiete, die im Behälter- und Apparatebau, in der Raumfahrt und im Rohrleitungsbau liegen.
Wie funktioniert Arcatom-Schweißen?
Das Aratom-Schweißen ist seit 1924 bekannt. Es wurde von Irving Langmuir erfunden und nutzt die Rekombinationsenergie, die sich im Wasserstoff befindet, um die Temperaturen für das Schweißen zu erhalten.
Dabei kommt ein Wasserstoffgas zum Einsatz. Dieses wird durch einen Lichtbogen geblasen, der zwischen zwei Wolframelektroden, der sogenannten Langmuir-Fackel, entsteht. Es entsteht atomarer Wasserstoff, der auf die Schweißstelle gerichtet wird. Dort bildet sich aus dem atomaren Wasserstoff, der aus nur einem Wasserstoffatom besteht, molekularer Wasserstoff, der aus zwei Wasserstoffatomen besteht. Das führt zu einer Freisetzung großer Mengen von Energie auf einer nur sehr kleinen Fläche. Die Temperaturen erreichen dabei bis zu 4.000 °C.
Zugleich wird das Material auf diese Weise von Wasserstoff umgeben. Dieses wirkt nun als Schutzgas und hält die Luft mit ihrem Sauerstoff fern. Auf diese Weise kann das Schmelzbad nicht oxidieren.
Was ist wichtig beim Punktschweißen?
Das Punktschweißen gehört zu der Gruppe des Widerstandsschweißens. Hierbei untergliedert sich das Schweißen selbst in verschiedene Prozesse, in denen Druck, Hitze und Strom zum Einsatz kommen. Dabei wird der elektrische Widerstand des Werkstückes selbst genutzt.
Das Werkstück wird unter Druck erhitzt. Dabei erreicht an den Berührungspunkten der elektrische Widerstand seinen größten Wert. Damit wird dann auch genau dort die meisten Energie in Form von Wärme freigesetzt.
Das Punktschweißen selbst wird vor allem für das Verschweißen von Blechen verwendet. Dabei werden zwei oder drei Bleche miteinander verbunden. Dafür liegen sich zwei Elektroden auf beiden Seiten der Bleche gegenüber. Sie drücken dann auf einen Punkt zusammen und leten dabei den Schweißstrom in das Blech.
Aufgrund des Druckes hat der Werkstoff genau zwischen den Elektroden an den Berührungspunkten den höchsten Widerstand und dort erfolgt dann auch sein Aufschmelzen. Der Widerstand beträgt am Übergang zwischen den Blechen rund das 30-fache des normalen Widerstandes des verwendeten Grundmaterials.
Die Elektroden befinden sich gewöhnlich auf einer Punktschweißzwange an deren Enden oder auf Zylindern. Damit die Elektroden selbst während des Vorganges nicht überhitzen, werden sie auf ihrer Innenseite mit Wasser gekühlt. Sie bestehen zumeist aus Kupfer oder Kupferlegierungen. Dadurch sind sie für Strom und Wärme sehr leitfähig. Das hält den Widerstand auch am Übergang zwischen der einzelnen Elektrode und dem Material des Werkstückes gering. Dieser beträgt dort nur das 5-fache des Widerstandes des Werkstückes.
Man muss beim Punktschweißen beachten, dass es zu Nebenschlüssen kommen kann. Dabei fließt der Strom über bereits geschweißten Punkte. Das bedeutet, dass an der eigentlichen Stelle entwickelt sich weniger Wärme, was zum Energieverlust und einer längeren Schweißdauer führt. Einer der Hauptanwendungsgebiete des Punkteschweißens ist der Automobilbau für das Verbinden von Karosserieteilen.
Was ist Rollennahtschweißen?
Das Rollennahtschweißen ist ebenfalls ein Verfahren des Widerstandsschweißens und es folgt in seiner Anwendung dem Prinzip des Punktschweißens. Anstelle einzelner Punkte wird hier jedoch durch das Rollen eine kontinuierlich durchgehende Naht erzeugt.
Was versteht man unter Buckelschweißen?
Auch das Buckelschweißen ist eine Methode des Widerstandsschweißens und es besitzt eine deutliche Ähnlichkeit mit dem Punkteschweißen. Der Unterschied ist, dass auf einem der zu verbindenden Werkstücke eine Erhöhung vorhanden ist. Das ist der sogenannte Schweißbuckel.
Nut der Buckel wird nun mit dem anderen zu verschweißenden Werkstück verbunden. Die Gestaltung des Buckels definiert den Bereich des Stromübergangs. Dabei benötigt man keine besondere Geometrie der Elektroden. Der Stromfluss und der Widerstand an der Übergangsstelle sorgen nun dafür, dass der Buckel zum Teil aufschmilzt und sich mit dem anderen Bauteil verbindet.
Wie funktioniert Unterpulverschweißen?
Das Unterpulverschweißen ist ein voll mechanisiertes Schweißverfahren mit einem Lichtbogen, welches sich vor allem aufgrund seiner hohen Abschmelzleistung auszeichnet. In der Industrie kommt es vor allem dort zum Einsatz, wo lange Nähte zu setzen sind.
Das Pulver im Unterpulverschweißen ist ein grobkörniges Mineral, dass den gesamten Prozess abdeckt. Durch die Hitze des Lichtbogens schmilzt auch das Pulver und es bildet sich eine flüssige Schlacke. Diese Schlacke hat eine geringere Dichte als das Schmelzbad. Das heißt, sie ist leichter als der Werkstoff und schwimmt daher auf diesem.
Die Schlacke dient nun dazu, das Schmelzbad vor dem Zutritt der Außenluft zu schützen. Der Lichtbogen selbst befindet sich in einer Kaverne unterhalb der Schicht aus Schlacke, die mit einem Gas befüllt ist. Ist der Schweißvorgang abgeschlossen, löst sich die Schlacke oftmals von ganz allein ab. Das Pulver kann man dann erneut verwenden.
Neben der hohen Abschmelzleistung, die mit diesem Verfahren erzielt wird, ist auch das weitgehende Fehlen von Emissionen ein weiterer Vorteil. Der Lichtbogen selbst brennt unterhalb der Pulverschicht, so dass nur sehr wenig Rauch austreten kann. Auch ist kein Sichtschutz während der Arbeit nötig.
Die sehr hohe Abschmelzleistung ergibt sich aus dem thermischen Wirkungsgrad. Die Abdeckung hält die Hitze innerhalb des Schmelzbades, anstatt sie schnell an die Umgebung abzugeben. Das führt aber auch dazu, dass mit diesem Verfahren man nur größere Blechdicken bearbeiten kann.
Darüber hinaus ist aufgrund der Abdeckung durch die Schicht Schlacke eine visuelle Kontrolle des Prozesses nicht möglich. Dennoch können damit sehr gute Schweißnähte mit einer hohen Qualität erreicht werden.
Was ist Laserstrahlschweißen?
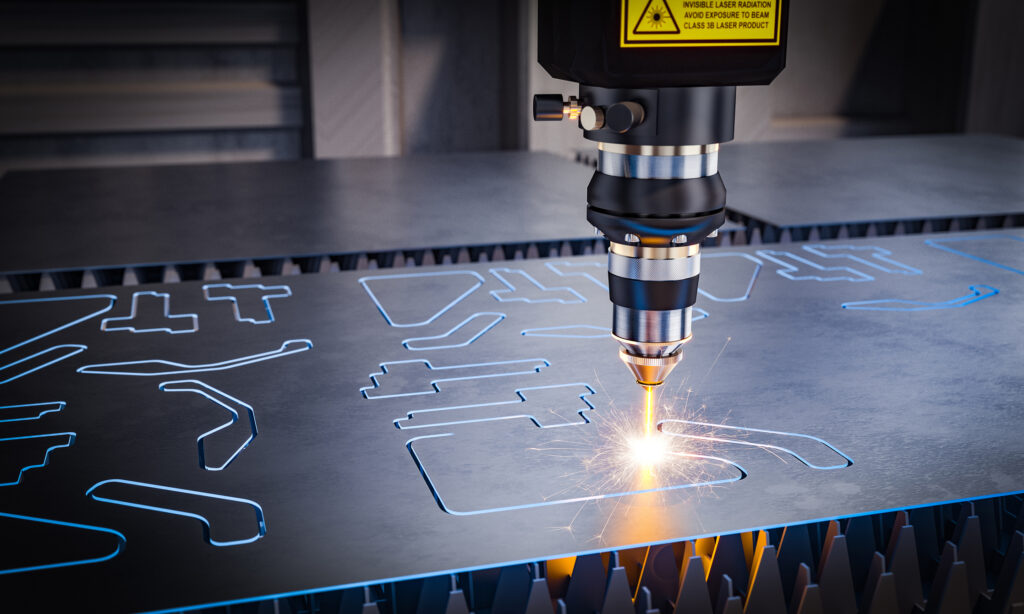
Das Laserstrahlschweißen erlaubt das genaue fokussieren der eingesetzten Energie. Damit ist es möglich, eine sehr hohe Schweißgeschwindigkeit zu erreichen. Auch ist die Form der Schweißnaht sehr schmal und schlank. Für das Werkstück ergeben sich dabei ein nur sehr geringer thermischer Verzug. Das Laser Schweißen kommt dabei gewöhnlich auch ohne einen besonderen Zusatzstoff aus.
Wie der Name „Laserstrahlschweißen“ bzw. „Laserschweißen“ es bereits verrät, kommt bei diesem Verfahren Licht zum Einsatz. Dieses konzentriert sich auf die Oberfläche der Stoßkante. Die Optik des Lasers befindet sich dicht an der Oberfläche und seine Ausrichtung legt unter anderem die Schweißtiefe fest.
Wie geht Elektronenstrahlschweißen?
Das Elektronenstrahl Schweißen verwendet für das Erhitzen der Werkstoffe einen Strahl aus Elektronen. Dieser wird durch eine Hochspannung im Bereich von 60 bis 150 kV erzeugt. Diese beschleunigt die beteiligten Elektronen und bildet aus diesen in einem Vakuum einen Strahl. Damit ist das Elektronenschweißen im wahrsten Sinne des Wortes ein Schweißen ohne Gas, ohne jede Form von Gas.
Treffen die Elektronen auf das Werkstück, wird ihre kinetische Energie in Wärme umgewandelt. Das Elektronenstrahlschweißen erlaubt es so, eine Leistungsflussdichte zu erreichen, die dem des Laserstrahlschweißens entspricht. Dabei ist jedoch der Wirkungsgrad deutlich höher. Dieser liegt für den Laser bei nur 3 bis 14%, während er für den Elektronenstrahl ungefähr 70% erreicht. Das ermöglicht es, mit einer sehr hohen Schweißgeschwindigkeit zu arbeiten. Zugleich sind die Schweißnähte extrem tief und äußerst schmal. Das wiederum führt dazu, dass der thermische Verzug extrem klein ist.
Anwendung Elektronenstrahlschweißen
Das Verfahren kommt vor allem bei sehr kleinen Schweißnähten zum Einsatz. Der Elektronenstrahl lässt sich mittels elektrischer Felder sehr genau kontrollieren, so dass er sich sehr präzise einsetzen lässt. Darüber hinaus ermöglicht die hohe Energiedichte auch das Verschweißen von Metallen, die eine sehr hohe Abschmelztemperatur aufweisen. Darüber hinaus können damit Mischverbindungen aus unterschiedlichen Materialien, zum Beispiel Stahl und Bronze, erstellt werden.
Die Weiterentwicklung der Technik, vor allem der Vakuumtechnik, macht das Verfahren inzwischen deutlich schneller. Es entfallen damit die langen Wartezeiten, die für das Herstellen des Unterdruckes gebraucht werden, weitestgehend. Darüber hinaus fehlen im Vakuum und in diesem Verfahren Gase, die den Prozess bzw. die Werkstoffe schädigen können. Damit lassen sich so auch Materialien verschweißen, die sonst hochreaktiv sind. Aufgrund des Vakuums befindet sich auch der Elektroschweißer außerhalb des Gefahrenbereichs der Radioaktivität.
Das Elektronenstrahlschweißen kommt oft in der Herstellung von Bauteilen für Getriebe innerhalb der Automobilindustrie zum Einsatz. Darüber hinaus sind die Luft- und Raumfahrt, der Schienenverkehr und die Lebensmittelindustrie weitere Felder, in denen sich dieses Verfahren bewährt hat.
Was versteht man unter Thermit-Schweißen?
Das Thermit- oder Aluminothermische-Schweißen verwendet man besonders im Bereich von Bahnschienen. Dabei wird mit einem Tiegel Eisenoxid- und Aluminiumpulver auf die Verbindungsstelle aufgebracht und mit einem Magnesiumspan entzündet. Das führt dazu, dass sich ein Bad aus flüssigem Eisen mit einer Schlacke aus Aluminiumoxid bildet, die die Schienen verbindet.
Was bedeutet Kaltpressschweißen?
Das Kaltpressschweißen erfolgt nicht mit Hitze, dafür aber mit hohem Druck. Dabei hält man die Temperatur noch unterhalb der Rekristallisationstemperatur der Werkstoffe der beteiligten Bauteile. Das heißt, die Werkstücke verbleiben in einem festen Zustand. Es gibt kein Abschmelzen und kein Schmelzbad. Tatsächlich erfolgt eine plastische Verformung aufgrund des Druckes.
Die Berührung der Kontaktflächen unter diesem Druck bringt die zwischenatomaren Bindekräfte in den Werkstoffen zur Wirkung, um eine stabile und dauerhafte Verbindung der beiden Werkstücke aufzubauen. Dabei braucht man eine Mindestverformung, die eine dauerhaft stabile Verbindung erst möglich macht. Das mit Materialien möglich, deren Kaltverformbarkeit groß genug ist. Dazu gehören Kupfer und Aluminium mit Bauteilen des eigenen oder jeweils anderen Werkstoffes.
Es ist sogar möglich, durch die aufgebaute Verbindung eine dauerhafte Stromleitfähigkeit zu erhalten. Dafür ist es jedoch hilfreich, die Werkstoffe vorzubereiten. Sie sollten entfettet und die Oxidschicht an der Oberfläche aufgerissen werden. Darüber hinaus ist es möglich, mit bestimmten Randbedingungen, zum Beispiel durch ein Hochvakuum, das Keramiken und Metallen im Kaltpressschweißverfahren miteinander dauerhaft und stabil zu verbinden.
Wie geht Reibschweißen?
Das Reibschweißen verschweißt zwei Bauteile mit durch Reibung erfolgter Erwärmung und mit einem hohen Druck. Dabei werden die Flächen, an denen die beiden Teile verschweißt werden sollen, gegeneinander bewegt. Die so entstehende Reibung sorgt für die Erwärmung.
Im nächsten Schritt werden dann die Flächen in der richtigen Lage zueinander mit einem hohen Druck aufeinandergepresst. Auch dieses Verfahren verzichtet auf ein Schmelzbad in den verschweißen Arealen. Damit ist die Einflusszone der Erwärmung deutlich geringer.
Was ist Rotationsreibschweißen?
Das Rotationsreibschweißen ist ein weiteres Verfahren des Pressschweißens. Für die Anwendung muss zumindest eines der beiden beteiligten Werkteile in der vorgesehen Füge Zone rotationssymmetrisch sein. Das heißt, egal, wie es rotiert, es muss in jeder Lage passen.
Von den beiden beteiligten Bauteilen wird eines fixiert und das andere gegen das erste Teil rotiert. Die Erwärmung und der anschließende Druck verschweißt dann die beiden an der Fügestelle. Damit werden zum Beispiel besonders gut Rohre und Bohrgestänge verbunden. Das geht auch, wenn beide Werkstücke über eine unterschiedliche Materialgüte verfügen.
Das Verfahren ist seit mehreren Jahrzehnten im Einsatz und wird auch gern beim Bau von Motoren verwendet. Innerhalb von Sekunden lassen sich damit feste Verbindungen aufbauen, wie zum Beispiel Auslassventile an Zylindern. Auch können so verschiedene Materialien, wie Stahl und Aluminium, verbunden werden.
Die für das Verfahren verwendeten Maschinen ähneln Drehmaschinen und haben eine Größe, die bei kleineren Geräten der eines Schreibtisches und bei größeren der einer Lokomotive entspricht. Sie verfügen über eine rotierende Spindel über einem fixen Gegenstück. Ein axial zustellbarer Schlitten erlaubt es, das zweite Teil auf das rotierende Teil zu drücken. Die Kräfte können dabei Druck erreichen, der mit einer Last von bis zu 1.000 Tonnen vergleichbar ist.
Wie funktioniert Reibrührschweißen?
Das Reibrührschweißen, auch als FSW für Friction Stir Welding bezeichnet, wurde 1991 in Großbritannien entwickelt und von Wayne Thomas patentrechtlich geschützt. Dieses Verfahren ähnelt dem Rotationsreibschweißen. Es wird für das Verschweißen von Blechen verwendet.
Diese werden nun mittels eines rotierenden Werkzeuges verbunden. Dieses plastiziert den Werkstoff. Das heißt, er ist noch nicht heiß genug, um abzuschmelzen, aber auch nicht mehr kalt genug, um fest zu sein. Das rotierende Werkzeug, ein Pin, kommt mit einem Gewinde, der das plastifizierte Material beider Werkstoffe vermischt und sie so verbindet. Es entsteht ein Extrusion Kanal, der sich bis zur Nahtwurzel erstreckt und auch oftmals als Schweißnugget bezeichnet wird.
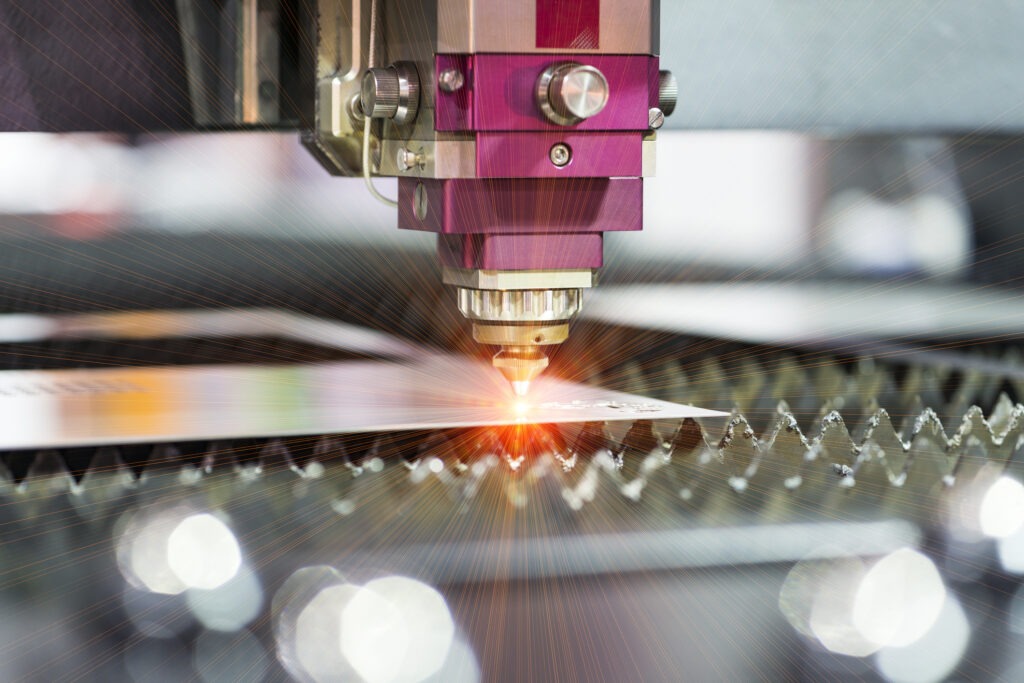
Was ist LAFSW-Schweißen?
Das Laser Assisted Friction Stir Welding gehört zur Technik des Reibrührschweißens. Als eine Variante wird hier jedoch das Werkzeug im Einsatz durch einen Laser unterstützt. Dieser bringt mehr Wärmeenergie in die Fügefläche ein, indem er dem Werkzeug vorauswandert. Das verringert die benötigte Kraft, um den Pin in das Werkstück einzuführen und erhöht damit Schweißgeschwindigkeit. Dies geht jedoch mit einem höheren Aufwand, vor allem in kostentechnischer Sicht, einher, denn es musste man hier auch noch in einen Laser investieren.
Wie geht Ultraschallschweißen?
Das Ultraschallschweißen ist ein Verfahren, mit dem sich Kunststoffe zusammenfügen lassen. Daneben ist es möglich, auch Metalle damit zu verschweißen. So wird dieses Verfahren in der Elektrotechnik verwendet, um Mikrochips zu verdrahten.
Was ist Sprengschweißen?
Das Sprengschweißen ist ein Verfahren, mit denen sich zwei Materialien, die normalerweise nicht verschweißbar sind, fest miteinander verbinden lassen. Der dabei verwendete Sprengstoff dient dazu, die beiden Schweißflächen mit einer hohen Geschwindigkeit in Richtung aufeinander zu beschleunigen. Dabei besteht ein Winkel von 2° bis 30° zwischen den beiden. Die erreichten Geschwindigkeiten liegen bei 100 Metern pro Sekunde oder darüber.
Aus der Kollision der beiden Teile ergibt sich ein erheblicher Energiefreisatz, der die Verbindung auf atomarer Ebene und sogar unter Einwirkung der Gitterkräfte der Metalle bewirken. Damit lassen sich Werkstoffe verbinden, deren Schmelztemperaturen sich normalerweise nicht erreichen lassen. So lässt sich damit zum Beispiel Kupfer mit Titan schweißen. Auch ist so das Schweißen ohne Schweißgerät möglich.
Für die Sprengwirkung kommen PETN-, HDX- und RDX-Sprengstoffe zum Einsatz. Dabei erreicht man Detonationsgeschwindigkeiten, die 5.000 Meter pro Sekunde überschreiten. Der Aufprall der Werkstücke aufeinander. Das sorgt für wellenartige Verwerfungen innerhalb der Materialien, die dann die formschlüssige Verbindung bilden.
Was versteht man unter Diffusionsschweißen?
Das Diffusionsschweißen ist seit rund 50 Jahren bekannt und wird dafür verwendet, vor allem Metalle zu verbinden. Die Qualität der Schweißnähte ist sehr hoch. Für das Verfahren selbst arbeitet man mit einem hohen Druck, die sich innerhalb der Fließgrenze bewegen. Damit verbinden sich die Flächen sehr glatt miteinander. Der Druck kann mittels einer Presse oder mittels eines Schutzgases in einer Druckkammer erzeugt werden.
Fazit
Es gibt eine ganze Reihe von Schweißtechniken, die den verschiedenen Anforderungen der Aufgaben gerecht werden. Das reicht von Feuerschweißen, dass sich mit relativ einfachen Mittel bewerkstelligen lässt, die keinen großen Fortschritt bedürfen, bis hin zum Laser- und Elektronenstrahlschweißen, die sich durch sehr starke Schweißnähte, die sehr schmal sind, auszeichnen. Damit steht für jeden Bedarf ein passendes Verfahren zur Verfügung.
Mehr über Schweißen:
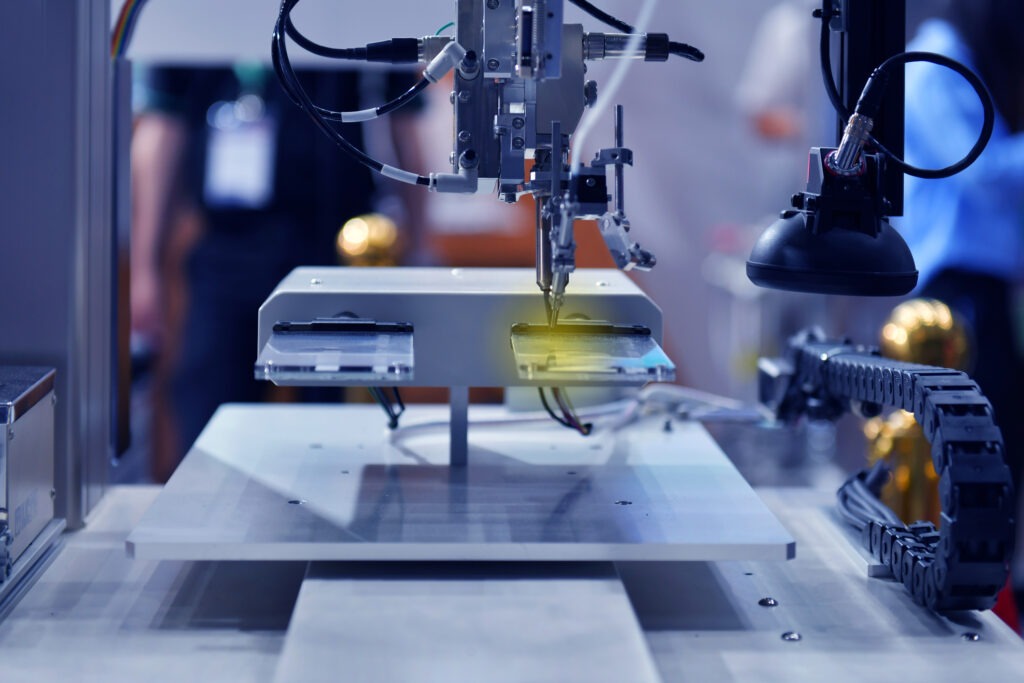