Welding process overview
Welding has come a long way and it is not surprising that it has moved in different directions. This has resulted in a whole range of different welding methods, which we would like to take a closer look at in this chapter in the form of an overview of welding processes
Table of contents
- Welding process overview
- What is hot-dip welding and how is it used?
- How does fusion welding work?
- What methods are used for joint, build-up, and path welding?
- How does gas metal arc welding (GMAW) work?
- What is tungsten inert gas welding (TIG)?
- What does plasma welding involve?
- How does Arcatom welding work?
- What should be considered when spot welding?
- What is roller seam welding?
- What is projection welding and how is it used?
- How does submerged arc welding (SAW) work?
- What is laser beam welding?
- How does electron beam welding work?
- What is meant by thermite welding?
- What is cold pressure welding?
- How does friction welding work?
- What is rotary friction welding?
- How does friction stir welding work?
- What is LAFSW welding?
- How does ultrasonic welding work?
- What is explosive welding?
- What is diffusion bonding?
Estimated reading time: 21 minutes
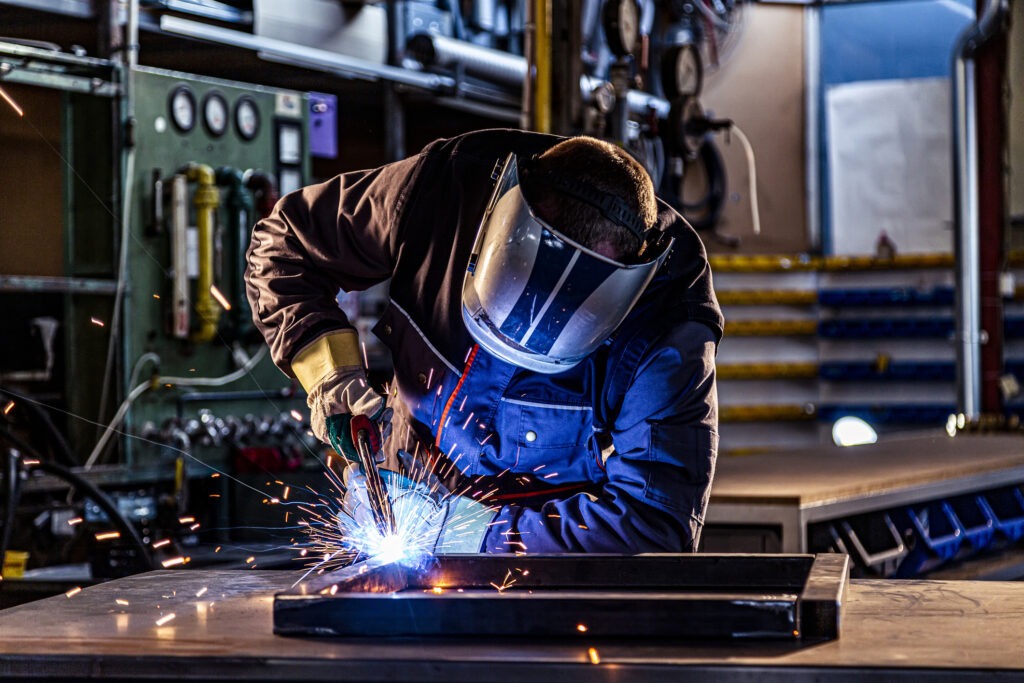

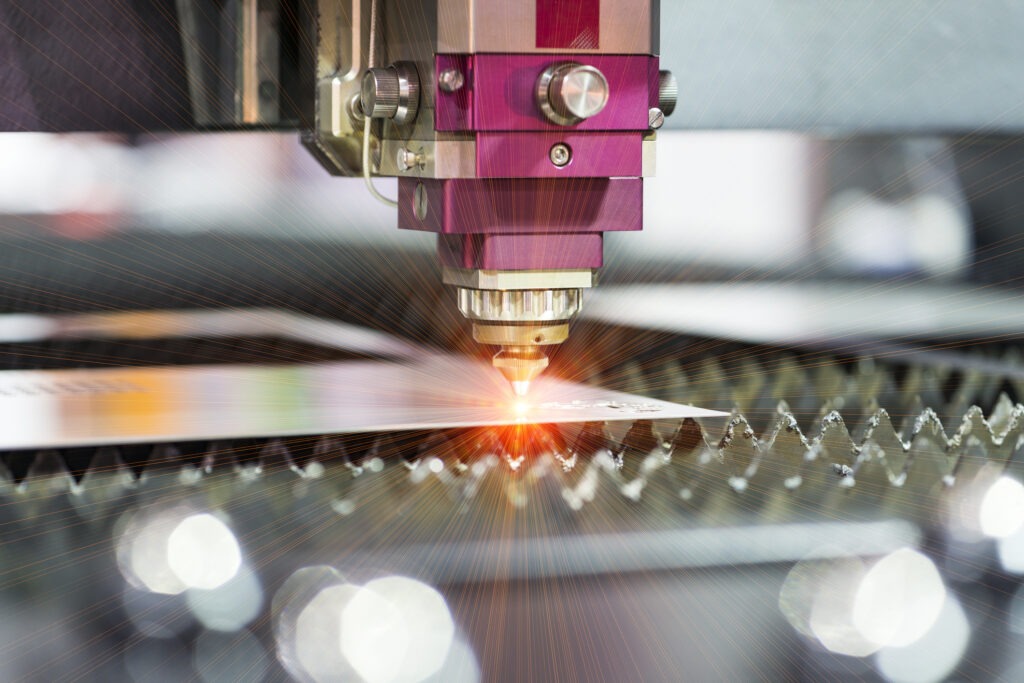
What is hot-dip welding and how is it used?
The oldest method of welding still known to this day is fire welding. Here, the metals that are to be joined are brought to a state that can be described as doughy in the fire under the exclusion of outside air. These parts were then joined under pressure. The pressure was generated with hammer blows, for example. It is important to be strong enough to build up sufficient pressure, but not too strong so that the parts do not bounce apart again immediately.
The temperatures during hot-dip welding are between 1200 and 1300 °C on the surface of the materials. The steel is not melted in the process. However, air must be prevented from penetrating so that it does not oxidise. This was initially achieved by using a fine-grained river sand. Although this achieved good air exclusion, it also made it difficult to achieve the correct melting point. Today, borax is used for this purpose. This creates a liquid skin that spreads over the steel parts and thus protects them from the penetration of air.
Fire welding was used by blacksmiths to produce weapons. It was used to make swords and daggers, for example, which were made from so-called Damascus steel.
How does fusion welding work?
In fusion welding, a melt flow is generated without the use of force. However, welding consumables can be used. It is important that after welding, the materials have the same properties after cooling as they had before heating.
Although fusion welding is mostly used for metallic materials, it can also be used for other materials. These include, for example, glass and glass fibres, as well as thermoplastics. Weld seams can also be created here. However, it is also possible to work with spot welds and welding surfaces, as with friction welding.
If fusion welding is used for steel, it should be noted that only simple steels with a carbon content of up to 0.22% C and a strength of 500 N/mm2 can be permanently joined. Steels that are alloyed or have a higher strength require further measures to prevent the formation of fractures and cracks.
Other measures include preheating, slow cooling, tempering or stress relief annealing. Special welding processes can also be used.
What methods are used for joint, build-up, and path welding?
Joint welding is used to join two workpieces. This is the case, for example, with a longitudinal pipe seam. Deposition welding, on the other hand, is the coating of a workpiece using a welding process. The materials for the workpiece and the build-up are different. This form of welding is mainly used for armouring, buffer layers and cladding.
Web welding is carried out with the help of robots. These weld materials automatically without further human intervention.
How does gas metal arc welding (GMAW) work?
Gas metal arc welding, or GMAW for short, which includes MIG and MAG, is an even more recent arc welding process. It was developed in the USA in 1948 and made it to Europe shortly afterwards.
Initially, inert gases or argon were used. These contained only small amounts of oxygen and other active components. This is why the process was initially called SIGMA welding. Sigma stood for "shielded inert gas metal arc".
However, inert gases were expensive and the Soviet Union did not want to bear the associated costs. For this reason, active gases, such as carbon dioxide, were also used there from 1953. This was made possible by the development of new wire electrodes. These electrodes took into account the fact that the elements of the alloys burnt off more with active gases.
The welding wire melts during the welding process. In order not to exhaust it, the wire is continuously fed by a motor. The speed of the motor can be adjusted.
What is tungsten inert gas welding (TIG)?
Tungsten inert gas welding is abbreviated to TIG in German. In English, however, the abbreviation TIG comes from the English word tungsten for tungsten. The process was introduced in the USA in 1936 as Argonarc welding. After the Second World War, it also became widespread in Germany.
TIG pulse welding
The TIG process also gave rise to TIG pulse welding. Pulsed current is used here, which allows the heat input into the workpiece to be very finely dosed. This makes gap bridging very easy. It also enables good root welding and facilitates welding in constrained positions. Weld seam defects, which often occur at the beginning or end of a seam, are also avoided.
TIG orbital welding
Orbital welding is a welding process in which a joint is produced with at least one round body. In most cases, this is a pipe. To do this, the arc is guided around the round body, which is fixed in place. The arc usually performs at least one full rotation without interruption, i.e. 360°.
The process belongs to the group of partially mechanised welding. The TIG method is used because it allows the weld pool to be kept very well under control. This means that the same rules apply to TIG orbital welding with regard to the cleanliness and weldability of the materials used as with all other TIG welding processes.
Orbital welding is also always important when the demands on the quality of the weld seam are particularly high. This is not just about strength, but also about X-ray safety and the shape of the weld seam. For many users, the main focus here is on low roughness coupled with an even and, above all, flat root. This also results in the areas of application, which range from pharmaceuticals to food and biotechnology.
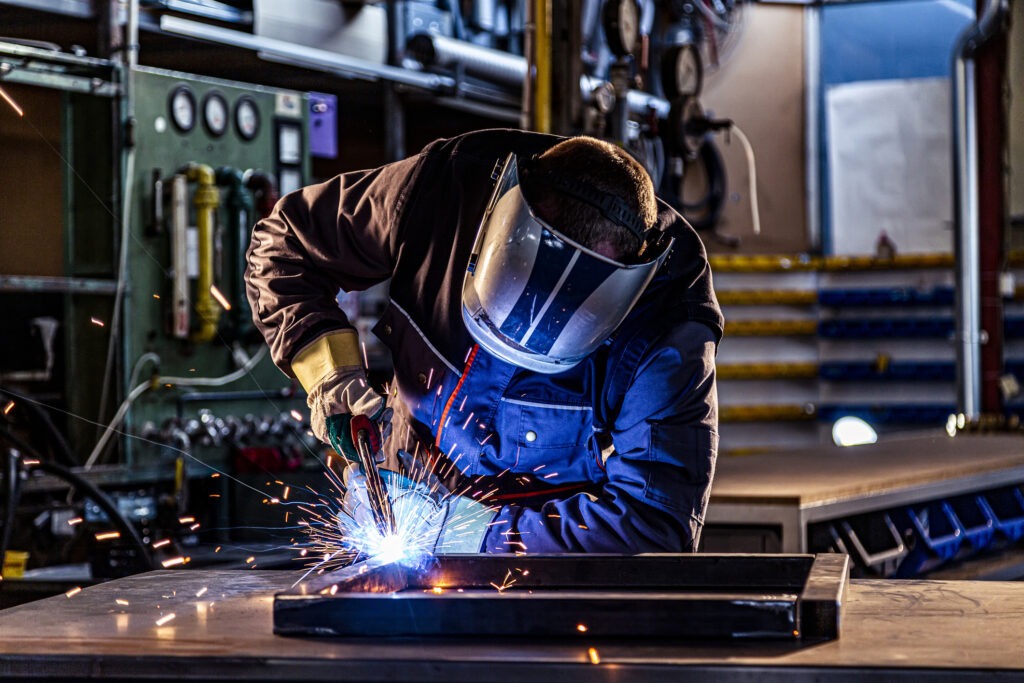
What does plasma welding involve?
Plasma welding uses a plasma jet as the heat source with which the material is melted. The plasma itself is a gas that is electrically conductive and is heated up using an electric arc.
Argon is used as the plasma gas in the plasma torch. This is ionised via high-frequency pulses and ignited with a pilot arc. The electrode is made of tungsten and has a negative polarity. The workpiece has a positive pole. A gas column is created between the two via a nozzle, which is ionised in the process. This allows the arc to be ignited without contact.
The plasma jet that forms the transferred arc is itself surrounded by a shielding gas. For example, argon is used, which contains 5% to 7% hydrogen. The shielding gas also helps to stabilise the arc and protects the molten pool from oxidation with the oxygen in the air.
The plasma arc created by the gas column is constricted by the copper nozzle used. This nozzle is permanently cooled with water to protect it from the heat. The gas column has an almost perfect cylindrical shape. This makes it possible to concentrate the energy used at the point of welding. This makes it possible to accelerate the melting process, resulting in a higher overall welding speed. This also reduces distortion of the workpiece and results in less stress.
The currents used can be very low and the plasma arc still burns stably below 1 ampere. It is also insensitive to changes in its length. This means that the distance between the nozzle and the workpiece has little influence, which also makes it suitable for use in micro welding. This means that even sheets with a thickness of just 0.1 mm can be welded. This results in the main areas of application, which are in tank and apparatus construction, aerospace and pipeline construction.
How does Arcatom welding work?
Aratomic welding has been known since 1924. It was invented by Irving Langmuir and utilises the recombination energy found in hydrogen to obtain the temperatures required for welding.
A hydrogen gas is used for this. This is blown through an arc that is created between two tungsten electrodes, the so-called Langmuir torch. Atomic hydrogen is produced, which is directed at the welding point. There, the atomic hydrogen, which consists of only one hydrogen atom, forms molecular hydrogen, which consists of two hydrogen atoms. This leads to the release of large amounts of energy in a very small area. The temperatures reach up to 4,000 °C.
At the same time, the material is surrounded by hydrogen in this way. This now acts as a protective gas and keeps the air and its oxygen away. In this way, the molten bath cannot oxidise.
What should be considered when spot welding?
Spot welding belongs to the group of resistance welding. Welding itself is subdivided into various processes in which pressure, heat and electricity are used. The electrical resistance of the workpiece itself is utilised.
The workpiece is heated under pressure. The electrical resistance reaches its highest value at the points of contact. This means that most of the energy is released in the form of heat right there.
Spot welding itself is mainly used for welding sheet metal. Two or three sheets are joined together. To do this, two electrodes are placed opposite each other on both sides of the sheets. They then press together at one point and conduct the welding current into the sheet metal.
Due to the pressure, the material has the highest resistance precisely between the electrodes at the contact points and this is also where it melts. The resistance at the transition between the sheets is around 30 times the normal resistance of the base material used.
The electrodes are usually located on a spot-welding clamp at their ends or on cylinders. To prevent the electrodes themselves from overheating during the process, they are cooled with water on the inside. They are usually made of copper or copper alloys. This makes them highly conductive for electricity and heat. This also keeps the resistance low at the transition between the individual electrode and the material of the workpiece. This is only 5 times the resistance of the workpiece.
When spot welding, it is important to note that shunts can occur. The current flows over spots that have already been welded. This means that less heat is generated at the actual spot, which leads to a loss of energy and a longer welding time. One of the main areas of application for spot welding is in the automotive industry for joining body parts.
What is roller seam welding?
Roller seam welding is also a resistance welding process and its application is based on the principle of spot welding. However, instead of individual spots, a continuous seam is created by rolling.
What is projection welding and how is it used?
Projection welding is also a method of resistance welding and is very similar to spot welding. The difference is that there is an elevation on one of the workpieces to be joined. This is the so-called welding projection.
The groove of the projection is now connected to the other workpiece to be welded. The design of the projection defines the area of the current transfer. No special geometry of the electrodes is required. The current flow and the resistance at the transition point now ensure that the projection partially melts and connects to the other component.
How does submerged arc welding (SAW) work?
Submerged arc welding is a fully mechanised welding process with an electric arc, which is primarily characterised by its high deposition rate. In industry, it is primarily used where long seams need to be created.
The powder in submerged arc welding is a coarse-grained mineral that covers the entire process. The heat of the arc also melts the powder and a liquid slag is formed. This slag has a lower density than the weld pool. This means that it is lighter than the material and therefore floats on it.
The slag now serves to protect the molten pool from the ingress of outside air. The arc itself is located in a cavern underneath the layer of slag, which is filled with a gas. Once the welding process is complete, the slag often detaches all by itself. The powder can then be reused.
In addition to the high deposition rate achieved with this process, another advantage is the almost complete absence of emissions. The arc itself burns below the powder layer, so that very little smoke can escape. There is also no need for visual protection during work.
The very high melting capacity results from the thermal efficiency. The cover keeps the heat inside the melting bath instead of quickly releasing it into the environment. However, this also means that this process can only be used to process thicker sheets.
In addition, visual inspection of the process is not possible due to the covering by the layer of slag. Nevertheless, very good weld seams with a high quality can be achieved.
What is laser beam welding?
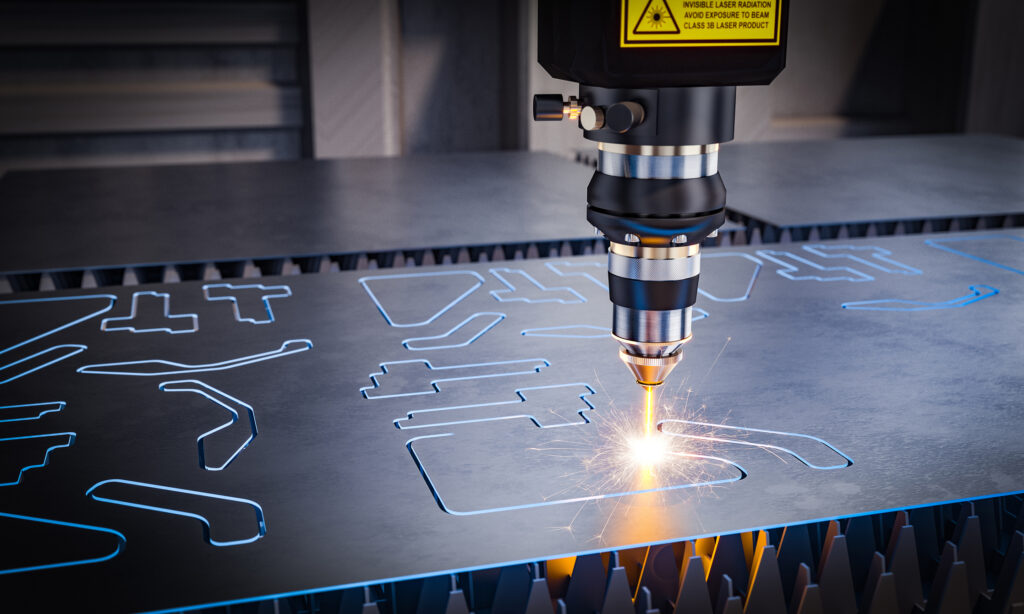
Laser beam welding allows the energy used to be precisely focussed. This makes it possible to achieve a very high welding speed. The shape of the weld seam is also very narrow and slim. This results in very little thermal distortion for the workpiece. Laser welding usually does not require any special filler material.
As the name "laser beam welding" or "laser welding" suggests, light is used in this process. This is focussed on the surface of the joint edge. The laser's optics are located close to the surface and its alignment determines the welding depth, among other things.
How does electron beam welding work?
Electron beam welding uses a beam of electrons to heat the materials. This is generated by a high voltage in the range of 60 to 150 kV. This accelerates the electrons involved and forms a beam from them in a vacuum. In the truest sense of the word, electron welding is therefore welding without gas, without any form of gas.
When the electrons hit the workpiece, their kinetic energy is converted into heat. Electron beam welding thus makes it possible to achieve a power flux density that corresponds to that of laser beam welding. However, the efficiency is significantly higher. This is only 3 to 14% for the laser, while it reaches around 70% for the electron beam. This makes it possible to work at a very high welding speed. At the same time, the weld seams are extremely deep and extremely narrow. This in turn means that the thermal distortion is extremely small.
Electron beam welding application
The process is primarily used for very small weld seams. The electron beam can be controlled very precisely by means of electric fields, meaning that it can be used very precisely. In addition, the high energy density also enables the welding of metals that have a very high melting temperature. It can also be used to create mixed joints from different materials, for example steel and bronze.
The further development of technology, especially vacuum technology, has now made the process significantly faster. This largely eliminates the long waiting times required to create the vacuum. In addition, there are no gases in the vacuum and in this process that could damage the process or the materials. This means that materials that are otherwise highly reactive can also be welded. Due to the vacuum, the electric welder is also outside the danger zone of radioactivity.
Electron beam welding is often used in the manufacture of components for gearboxes within the automotive industry. Aerospace, rail transport and the food industry are other fields in which this process has proven its worth.
What is thermite welding?
Thermite or aluminothermic welding is used particularly for railway tracks. In this process, iron oxide and aluminium powder is applied to the joint using a crucible and ignited with a magnesium chip. This results in the formation of a bath of molten iron with a slag of aluminium oxide, which connects the rails.
What is cold pressure welding?
Cold pressure welding is not carried out with heat, but with high pressure. The temperature is kept below the recrystallisation temperature of the materials of the components involved. This means that the workpieces remain in a solid state. There is no melting and no melt pool. In fact, plastic deformation occurs due to the pressure.
The contact of the contact surfaces under this pressure brings the interatomic bonding forces in the materials into effect in order to create a stable and permanent connection between the two workpieces. This requires a minimum deformation that makes a permanently stable bond possible in the first place. This is possible with materials whose cold formability is high enough. These include copper and aluminium with components made of the same or different materials.
It is even possible to achieve permanent electrical conductivity through the connection created. However, it is helpful to prepare the materials for this. They should be degreased and the oxide layer on the surface should be torn open. In addition, it is possible to join ceramics and metals permanently and stably using the cold pressure welding process under certain boundary conditions, for example using a high vacuum.
How does friction welding work?
Friction welding welds two components by heating them by friction and applying high pressure. The surfaces where the two parts are to be welded are moved against each other. The resulting friction provides the heating.
In the next step, the surfaces are then pressed together in the correct position using high pressure. This process also dispenses with a weld pool in the welded areas. This means that the zone of influence of the heating is significantly smaller.
What is rotary friction welding?
Rotational friction welding is another method of pressure welding. For this application, at least one of the two workpieces involved must be rotationally symmetrical in the intended joining zone. This means that no matter how it rotates, it must fit in every position.
One of the two components involved is fixed and the other is rotated against the first part. The heating and subsequent pressure then welds the two together at the joint. This is a particularly good way of joining pipes and drill rods, for example. This also works if the two workpieces have different material qualities.
The process has been in use for several decades and is also popular in the construction of engines. It can be used to create strong connections within seconds, such as exhaust valves on cylinders. It can also be used to join different materials such as steel and aluminium.
The machines used for the process are similar to lathes and are the size of a desk for smaller devices and a locomotive for larger ones. They have a rotating spindle above a fixed counterpart. An axially adjustable slide allows the second part to be pressed onto the rotating part. The forces can reach pressures comparable to a load of up to 1,000 tonnes.
How does fusionwelding work?
Friction stir welding, also known as FSW for Friction Stir Welding, was developed in the UK in 1991 and patented by Wayne Thomas. This process is similar to rotary friction welding. It is used for welding sheet metal.
These are now joined using a rotating mould. This plasticises the material. This means that it is not yet hot enough to melt, but also no longer cold enough to be solid. The rotating tool, a pin, comes with a thread that mixes the plasticised material of both materials and thus connects them. The result is an extrusion channel that extends to the root of the seam and is often referred to as a weld nugget.
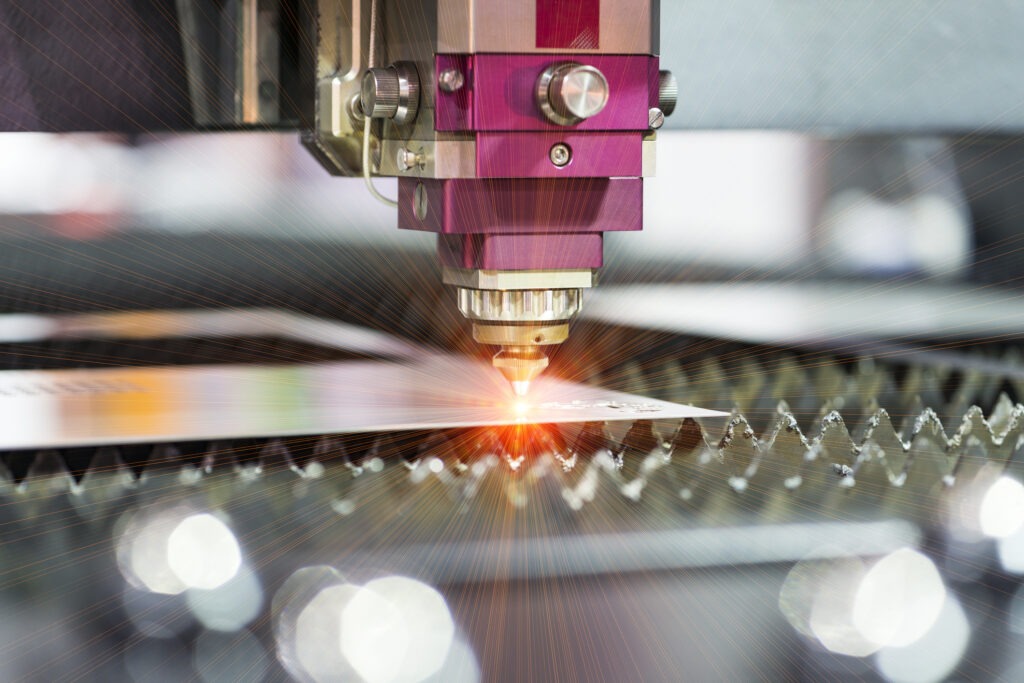
What is LAFSW welding?
The Temporary Laser Assisted Friction Stir Welding is part of the friction stir welding technique. As a variation, however, the tool is supported by a laser during use. This introduces more thermal energy into the joining surface by travelling ahead of the tool. This reduces the force required to insert the pin into the workpiece and therefore increases the welding speed. However, this comes at a higher cost, especially from a cost perspective, as you also have to invest in a laser.
How does ultrasonic welding work?
Ultrasonic welding is a process that can be used to join plastics. It can also be used to weld metals. For example, this process is used in electrical engineering to wire microchips.
What is explosive welding?
Explosive welding is a process by which two materials that cannot normally be welded together can be firmly joined. The explosive used in this process serves to accelerate the two welding surfaces towards each other at a high speed. There is an angle of 2° to 30° between the two. The speeds achieved are 100 metres per second or more.
The collision of the two parts results in a considerable amount of energy being released, which causes the connection at an atomic level and even under the effect of the lattice forces of the metals. This allows materials to be joined whose melting temperatures cannot normally be reached. For example, copper can be welded to titanium. Welding without a welding machine is also possible.
PETN, HDX and RDX explosives are used for the detonation effect. Detonation speeds in excess of 5,000 metres per second are achieved. The impact of the workpieces on each other. This creates wave-like distortions within the materials, which then form the positive connection.
What is diffusion bonding and how does it work??
Diffusion bonding has been known for around 50 years and is used to join metals in particular. The quality of the weld seams is very high. The process itself involves working with a high pressure that is within the yield point. This allows the surfaces to join together very smoothly. The pressure can be generated using a press or a shielding gas in a pressurised chamber.
Conclusion
There is a whole range of welding techniques that fulfil the various requirements of the tasks. These range from flame welding, which can be achieved with relatively simple means that do not require any major advances, to laser and electron beam welding, which are characterised by very strong weld seams that are very narrow. This means that there is a suitable process for every requirement.
More about welding:
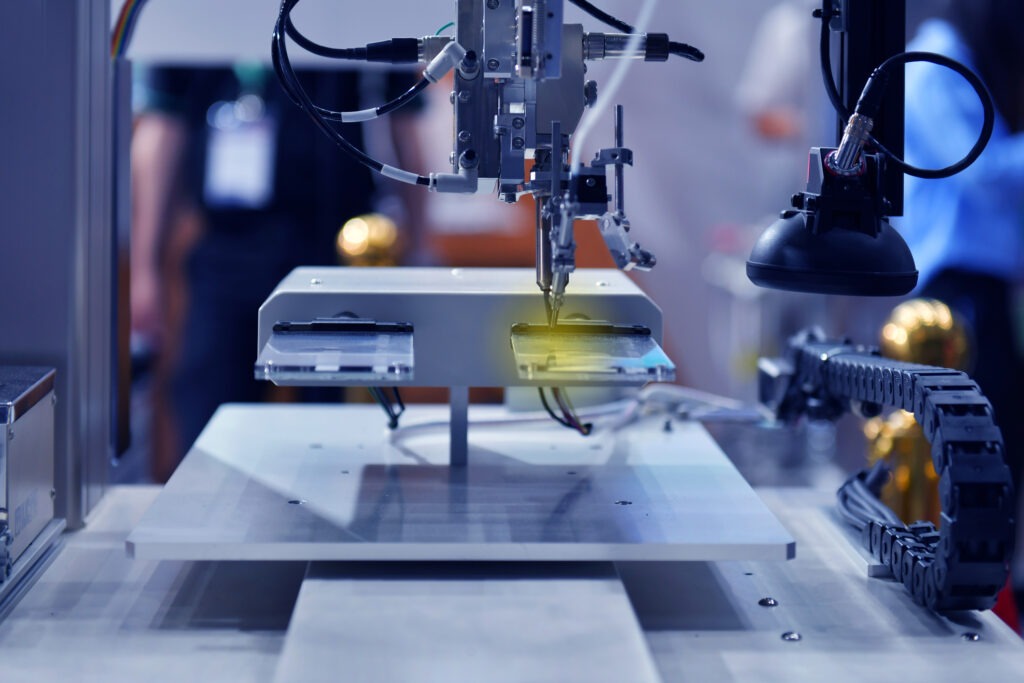