Shortage of skilled labour in production: causes, effects and solutions
The shortage of skilled labour is hitting the manufacturing industry particularly hard. In almost all branches of industry, there is a lack of qualified specialists. This shortage not only has an impact on the economy, but also on the Germany's capacity for innovation. Why is that? Because production is the backbone of our industry.
In this article we talk about the industry sectorsthat are most affected. We take a look at which Professions are missing and why. We also check which Measures Company against the shortage of skilled labour can take. And of course we ask the question: Are international specialists the solution?
- Shortage of skilled labour in production - affected industries and professions
- Causes of the shortage of skilled labour.
- Impact on the companies concerned
- Solutions and measures to combat the shortage of skilled labour
- Skilled workers from abroad as a solution to the skills shortage
- Favourite countries of origin for foreign skilled workers
- Requirements and challenges for the integration of foreign skilled workers
- Potential and limits of immigration as a solution to the shortage of skilled labour
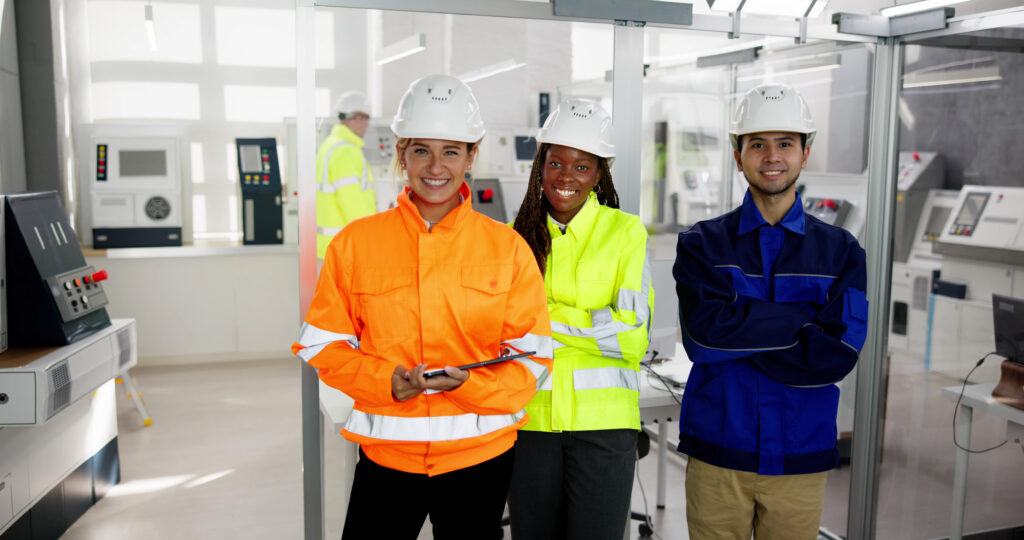
Welche Branchen und Berufe sind stark betroffen?
In the production there are many Sectorsespecially under the shortage of skilled labour suffer. Here we show you a Industry overview. These include, among others:
- Mechanical engineering
- automotive industry
- electrical engineering
- Chemical industry
- Food production
These industry sectors are the crux of the German economy. If here Labour force missing, this has huge consequences.
What are the affected professions? They are not only Engineersbut also specific Technical specialiststhat are missing. Professions like Machine and plant operator, industrial mechanics, electronics technicians and welders are in short supply. Even in the Quality control there is Bottlenecks. These are Professionswho are difficult to replace, as they require specialised knowledge and qualifications require.
According to Statistics from the Federal Employment Agency stay Jobs in these Called unoccupied for an average of 120 days - almost twice as long as in other Called. This shows how serious the Problem is.
Was sind die Ursachen für den Fachkräftemangel in der Produktion?
The shortage of skilled labour is anything but a coincidence, but the result of the interplay of several Factors. A look into the Demographic development already reveals a lot: The German population is ageing rapidly, while the Birth rate is falling steadily. This development also means that the number of young peoplenew to the labour market massively downwards. More and more Professionals say goodbye to their well-deserved Retirement - and unfortunately the Young talent often off. A Vicious circleyear after year, the production noticeably.
Education and Career choice also make a major contribution to the shortage of skilled labour with. Young people increasingly have academic Professions in our sights, while technical Professions and manual activities often fall on deaf ears. A Engineering studies or a Job in marketing sounds far more attractive to many than a Education to the industrial mechanics. The Problem? There are fewer and fewer Specialists for production trained. If the number of Apprentices naturally also lacks the necessary resources in the following years. Professionals on the shop floor.
In addition, the Technological change added. The startup digitisation and Automation are progressing and are Production landscape on the head. In the past, it might have been enough to Operate machine today, many tasks require specialised Knowledge of technology and digital skills. The Production industry urgently needs people with Expertise in modern Technologies - but the Training centres lag behind in terms of the necessary digital capabilities concerns. This is how Gapswhich are difficult to close.
After all, the Working conditions in production a major role. Shift work, Physically demanding activities and often a hectic pace are part of everyday life here. For many young people who want flexible and "Work-life balance-friendly" workplaces prefer, these conditions are a Exclusion criterion. Why invest in a Industry which is strenuous and challenging, even if it is also Jobs that are more Flexibility and less physical strain? The Competition for labour is getting harder and harder - and the production often gets the short end of the stick.
Welche Auswirkungen hat es auf die betroffenen Unternehmen?
Production delays are probably among the most painful Consequences. When Teams are chronically understaffed, the Work flow significantly slower. And this is not without consequences. Delays add up, Delivery dates cannot be maintained, and in the worst-case scenario, disgruntled Customers from. What for the Customers is a nuisance, it can be a Company end dramatically, because not only Orders are at risk, but also the Reputation and Customer loyalty.
The startup costs also increase if Professionals are missing. In order to Production gaps to close the gap, many Company options. Temporary work or Overtime back. However, this is expensive and eats away at the already strained Profit margins. The search for qualified Specialist in turn costs money and ties up resources that are not available for day-to-day business. In short: the shortage of skilled labour becomes a burden for the entire company balance sheet.
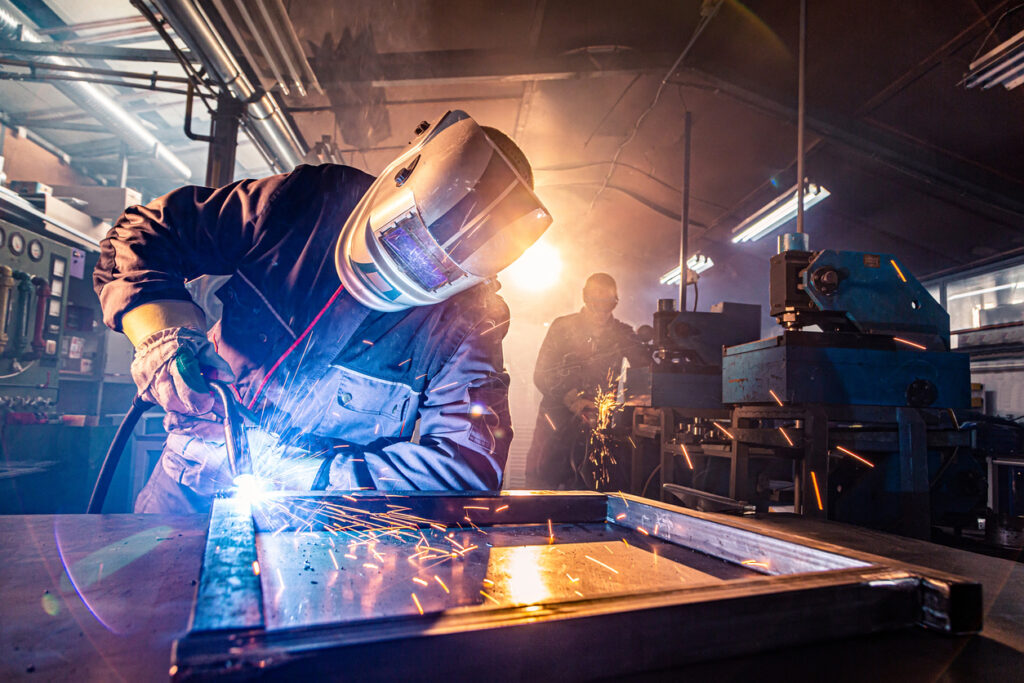
But the shortage of skilled labour not only costs time and money, but the quality of the products often suffers as well. Without experienced production staff, the error rate increases and Quality standards cannot be met. This leads to an increase in Returns and complaintsthat destroy customer confidence. It's actually a vicious circle: the worse the qualityThe lower the customer loyalty, the more difficult it will be to remain competitive in the market.
Was sind weitere Nachteile?
What about innovation? This also falls by the wayside. Without suitably trained staff, many companies lack the ideas and the knowledge of how New processes can be developed to work with new technological trends to be able to keep pace. This could Production facilities The future will be more efficient, more modern and more automated, but without the right specialists, many of these visions remain stuck in theory. As a result, companies not only lag behind, but in the worst-case scenario lose their Competitive advantagel.
One example illustrates this problem particularly clearly: a renowned Mechanical engineering company in Baden-Württemberg was recently forced to postpone several major orders. The reason? There was simply a lack of industrial mechanicsto manufacture and deliver the machines on time. The competition struck cold and secured the orders. A clear Competitive disadvantagewhich shows how urgently the production industry needs new solutions to meet the shortage of skilled labour master.
Here is some interesting information on mechanical engineering in production: "The myth of mechanical engineering studies: "Nothing is too difficult for an engineer"
There is also the branch of production specialists in chemistry. Find out more here: Chemical production specialist - training - profession.
Wie sehen Lösungsansätze und Maßnahmen zur Bekämpfung des Fachkräftemangels aus?
How can Company on the shortage of skilled labour react? Here are some promising ones Approaches:
- Training offensivesMore Apprenticeships and a narrower Exchange with schools and Vocational schools are necessary. Apprentices must start early for Technical professions be inspired.
- Further training for existing employees: The rapid development of technologies requires Regular training courses. Companies could support their employees with targeted Training programmes up to date.
- More attractive working conditions: Flexible working hoursbetter pay and a company pension scheme Health management could make jobs in production more attractive.
- Using digitalisation: The introduction of Robotics and artificial intelligence can take over routine tasks and free up more time for more demanding tasks.
- Rethink recruitment strategies: actively search for talent and approach potential specialists.
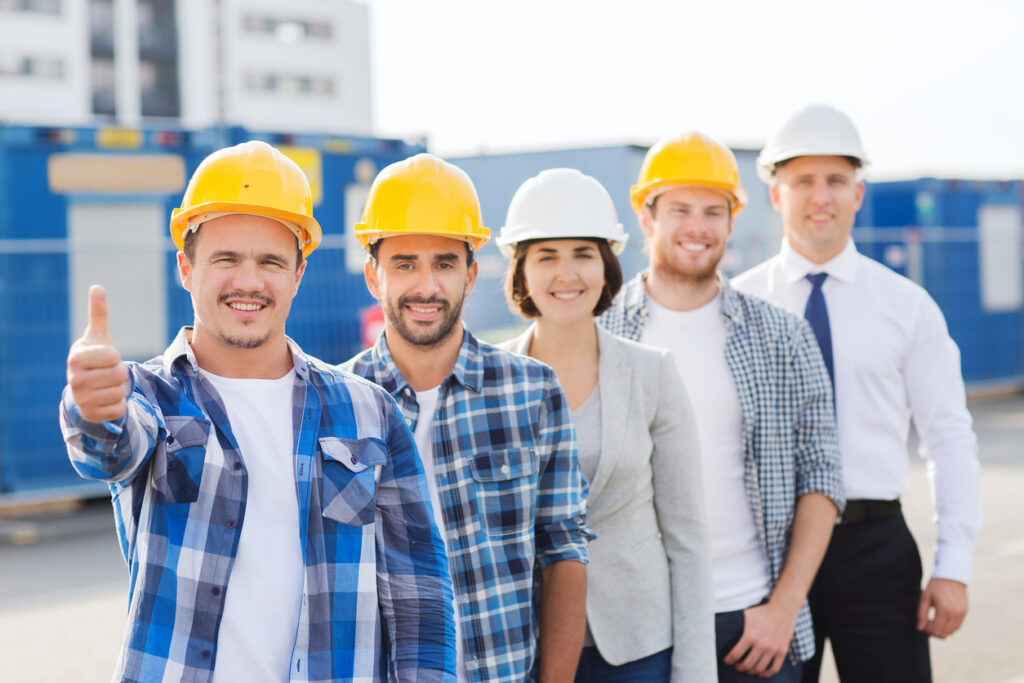
Sind Fachkräfte aus dem Ausland die Lösung für den Fachkräftemangel?
In view of the shortage of skilled labour foreign labour force increasingly important. But why should companies Professionals from abroad adjust?
- benefits—: International specialists often bring new Perspectives and a higher Motivation with. You have specialised Skillsthat are lacking in this country. In addition, many of them have excellent technical training and are prepared to work in the production to work.
- challenges.: Of course there are also Obstacles, how Language barriers and cultural differences. But Company these challenges. through Language courses and intercultural training overcome.
According to a Study by the Bertelsmann Stiftung is the share foreign skilled labour in the production has risen by 25 % in recent years. A clear sign that the Recruitment abroad worthwhile.
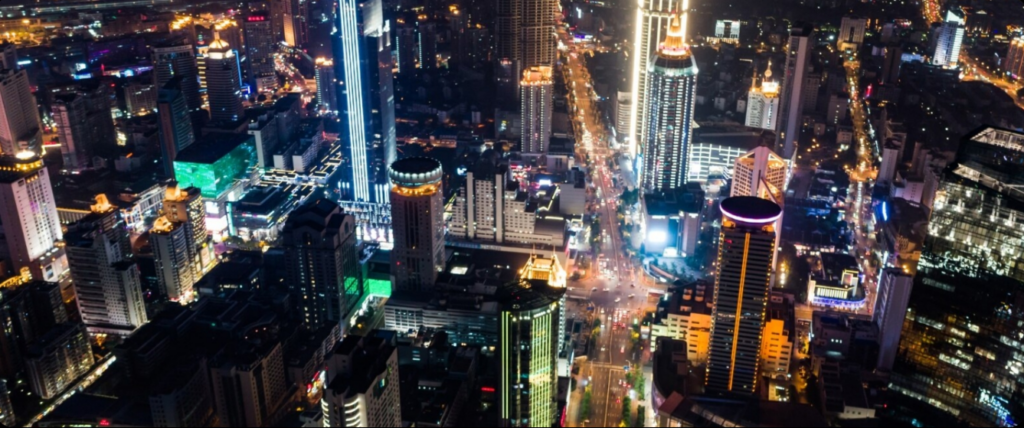
Welche sind beliebte Herkunftsländer für ausländische Fachkräfte?
Which Countries are particularly interesting for German companies? Here a Overview:
- EU countries: Many Company rely on Professionals out of Poland -, Slovakia, -, Romania, - and Bulgaria. This Countries have well-trained Labour forceand the Mobility within the EU facilitates the Entry into Germany.
- Non-EU countries: India and Philippines are known for their qualified Specialists in technical professions. Also Mexico and Vietnam are considered promising Countries.
- ChinaThe Training in technical professions has in China a high value, and many Professionals are prepared to Europe to draw.
Was sind Voraussetzungen für die Integration ausländischer Fachkräfte?
The startup Integration from international specialists provides Company before certain challenges.. But with the right Measures this can be mastered:
- Visa and work permitsFor Skilled workers from non-EU countries is a Work permit necessary. The Skilled Labour Immigration Act facilitates this Process.
- Language requirements: Language courses are for foreign skilled labour often absolutely necessary, especially in the production. Company can provide support here.
- Recognition of qualificationsThe foreign qualifications must often first recognised become. This Process can Time costs, but is necessary to ensure that the Professionals the necessary Skills bring along.
- Support and integration: Buddy programmes, Mentoring and intercultural training facilitate the Familiarisation.
Welches Potenzial und Grenzen hat die Einwanderung als Lösung des Fachkräftemangels?
The startup Immigration can not all Problems solve. However, it is an important Supplement to the internal measures. But what is the Long-term perspective?
- SustainabilityThe Recruitment abroad should be realised through an improved Education and higher Incentives for technical professions be supplemented. Only in this way can a Long-term solution be created.
- risksToo strong Dependence on international skilled labour the Further training of domestic labour neglect.
- Vision of the future: Business and politics have to work together to Production in Germany stable and competitive.
Innovationskraft durch Diversität: Wie bereichern internationale Fachkräfte die Produktion?
The startup Integration of international specialists into the production brings not only personnel Reliefbut also new Innovative strength with it. Why? Diversity in the teams promotes Creativity and encourages the exchange of different ways of thinking. Employees from other cultures and with different professional backgrounds bring new methods to the table. Problem solution and often valuable technical perspectives from their home country. They enrich the Production processes with ideas that would probably not have been expressed by traditional teams.
Research results prove this Effect. Diversity within a company has been shown to react more sharply to Market changes and is more innovative. This can be proof of the successful implementation of new Production techniques and working methods be the foreign skilled labour from their training and experience. It is not uncommon for a combination of local knowledge and international approaches to lead to new creative solutions that increase efficiency and Production quality increase.
Another argument in favour of diversity and international expertise could be that an internationally oriented team is much better equipped to deal with global partners, customers or suppliers. This is an obvious advantage in the age of globalisation. This is how Company twice - through the direct expertise and the improved Market adjustment. Companyadherence Actively promoting diversity and in Intercultural training invest, create a attractive and Innovative working environmentwhich in the long term will also young talents remains interesting.
Automation and artificial intelligence: replacement for skilled labour or support?
Automation and Artificial intelligence are no longer the sound of the future in the manufacturing industry. More and more companies are opting for Intelligent machinesthat can perform routine and physically demanding tasks. Whether the technology actually offers a shortage of skilled labour is not the case - at least not as a whole. Instead Machines andI to provide effective support for human Professionalsby reducing their workload and making their work more effective.
Robots are increasingly taking on light assembly tasks or the Quality control in production systems. In return, skilled workers gain time for more complex tasks that require analyses and problem solving. Also AI-supported Systemslarge amounts of data from production processes in real time support the specialists. This enables them to detect potential sources of error before they lead to production downtime. Human employees thus become analysts and decision-makers who control and optimise technical processes.
Another advantage of the Human-machine co-operation is that companies can react more flexibly to market changes. This allows companies to Skilled labour shortagel maintain or even expand production. Looking to the future, it is likely that production will be hybrid will remain: Humans and machines will work together in close cooperation, with skilled workers continuing to provide the expertise and decision-making. AI and robotics continue to perform the routine tasks. Only these Hybrid mode of operation can be the solution for the long-term mitigation of the Shortage of skilled labour and securing the innovation potential of production.
Wie können Produktionsprozesse durch gezielte Personalentwicklung optimiert werden?
The best answer to the shortage of skilled labour in the manufacturing industry, however, is clearly a targeted Personnel development in the companies. This enables production employees to learn new skills through needs-based training and further education. Expertise that better fulfil the changed requirements. In addition, the adaptation of the existing qualifications The new digitalisation of production processes helps to close the gap between traditional and digital skills while ensuring the quality and efficiency of manufacturing processes.
Wie kann nachhaltige Produktionskultur gefördert werden?
In view of the increasing shortage of skilled labour, a sustainable Production culture increasingly important. A working environment that is based on appreciation, security and Work-life balance increases employee loyalty and makes jobs in production more attractive. Through operational Health programmes, Flexible shift models and a conscious approach to workloads can help the production increase their attractiveness for existing and potential skilled labour. A sustainable Production culture also promotes innovative strength and the willingness to continuously improve - two decisive factors for surviving in a highly competitive environment.
Wie kann Effizienzsteigerung durch intelligente Schichtplanung und Automatisierung erreicht werden?
The manufacturing industry is faced with the challenge of shortage of skilled labour without jeopardising productivity. Intelligent shift planning in combination with modern Automation solutions can significantly increase efficiency and at the same time reduce the workload of existing employees. Through the strategic use of Automation With repetitive, physically demanding tasks, companies can free up their skilled labour for more complex activities. Balanced shift planning that caters to the needs of employees also increases job satisfaction and reduces staff turnover. The intelligent organisation of work processes is therefore a sustainable solution to the challenges of the Shortage of skilled labour in production.
Welche attraktiven Karrierewege gibt es zur Gewinnung und Bindung von Produktionsfachkräften?
In order to shortage of skilled labour counteract this in the long term, it is crucial to have clear and attractive Career paths in the production to create. If production employees see prospects for career advancement and targeted further development, they are more likely to be motivated to stay with the company and play an active role. The introduction of career levels and the opportunity to specialise or take on management tasks can increase the attractiveness of Workplaces in production increase. Such development opportunities create a win-win situation in which companies can rely on motivated specialists who contribute to long-term stability and innovative strength.
Wie können Arbeitsplätze an ergonomische Standards angepasst werden?
Due to the increasing Shortage of skilled labour it is becoming increasingly important to design production workstations ergonomically in order to minimise the physical strain on employees. Companies that work in Ergonomic work equipment and customised work processes not only protect the health of their skilled workers, but also increase the productivity and efficiency of their processes. Ergonomic measures can reduce sickness-related absences, which is particularly important in times of a shortage of skilled labour. In addition, the implementation of ergonomic standards employees that the company values their safety and well-being, which has a positive effect on job satisfaction and loyalty.
Wie funktioniert Kooperationen mit Bildungseinrichtungen für Nachwuchsförderung?
Proactive cooperation with Educational institutions is another effective approach to counteract the Shortage of skilled labour in production to counteract this. Through Partnerships with vocational schools, universities and technical colleges, companies can discover talented individuals at an early stage and recruit them for Production professions inspire. Such Co-operations make it possible to offer practical training and dual study programmes. These prepare young people for the demands of production. In addition, these partnerships create a pipeline of well-trained junior staff who can cover the future demand for skilled labour.
Wie kann ein flexibles Arbeitsmodell zur Steigerung der Mitarbeiterzufriedenheit helfen?
It is becoming increasingly important to Working models in production that cater to the needs of professionals. Flexible working hours and modern working models can increase employee satisfaction and thus promote their long-term loyalty to the company. By responding to the life situation of their employees, companies increase the attractiveness of the manufacturing industry as an employer. Possible flexible working models include
- Part-time and shift modelswhich can be customised to individual requirements.
- Flexitime options for a better work-life balance.
- Job sharing models (a position in which two (or more) employees share a full-time position) in certain production areas to reduce physical and mental stress.
With such flexible approaches, companies can mitigate the shortage of skilled labour in the long term and position themselves as a modern employer that understands the needs of its employees.
Wie wird innovative Unternehmenskultur gefördert?
An innovation-friendly Corporate culture can contribute to the shortage of skilled labour in the production and to increase the incentive for new specialists. A culture that emphasises openness, creativity and continuous improvement encourages employees to contribute new ideas and actively participate in the development of the company. Measures to promote such a culture can include
- Ideas competitions and employee initiatives for the improvement of production processes
- Interdisciplinary training courses and Workshopsthat strengthen the innovation expertise of the workforce
- Transparent communication and flat hierarchies, that enable better employee involvement and participation
A culture like this creates a motivating environment in which employees feel valued and actively drive the company forward - a significant advantage in times of a shortage of skilled labour.
Was ist proaktive Arbeitgebermarkenbildung für die Produktionsbranche?
The development of an attractive Employer brand in the manufacturing industry can also be a decisive factor in helping the shortage of skilled labour to counteract this. Companies that present their brand as more attractive Employer companies can position themselves better in the competition for skilled labour and retain qualified employees in the long term. A strong employer Branding in production can be achieved through various measures:
- Involvement of employees into the brand image through Employee portraits and Success stories.
- Transparent communication about career opportunities and working conditions on the company website and in social media.
- Partnerships with regional and international educational institutions to present the company as an attractive employer and attract young talent at an early stage.
With a convincing employer brand, companies are able to attract and retain talented specialists in the long term.
Wie hilft technologiegestützte Rekrutierung zur Optimierung des Einstellungsprozesses?
The use of modern Technology solutions in the Recruitment process can help companies to find suitable candidates more quickly and in a more targeted manner. Through the use of artificial intelligence (AI) and automated applicant management systems, job adverts can be placed in a targeted manner and application processes accelerated. At the same time, with the help of Data analytics better identify potential skilled workers and match their qualifications precisely with the requirements of production positions.
With a technology-supported recruitment companies can respond more quickly to labour shortages and attract the right talent to help secure their production targets in the long term.
Conclusion
The shortage of skilled labour poses major challenges for the manufacturing industry, with far-reaching economic consequences. Companies need to take proactive measures, ranging from targeted Training and further education to the integration of international specialists and automation. With a strong Employer brandbetter working conditions and innovative technologies companies can attract and retain skilled labour in the long term in order to secure their competitiveness and innovative strength.
Zeitarbeit International - Your personnel consultancy and recruitment agency for production specialists
Zeitarbeit International can provide companies with targeted support in personnel consulting and the recruitment of production specialists in order to effectively overcome the shortage of skilled labour. With a broad network and specialised Recruiting teams we have the necessary experience and Market expertiseto find qualified specialists.
From the targeted approach international talentsapplicant management and the Integration of new employees offers Zeitarbeit International - customised solutions that cover the entire Recruiting process facilitate the transition. Companies benefit from the rapid filling of vacancies, increased flexibility in personnel planning and a smooth transition to everyday production. In this way, we help to increase productivity and competitiveness in the German labour market. Production industry in the long term. Contact us today so that we can help you find production specialists for your company.