What is welding?
Welding is something everyone has heard of and most of us have seen it at least in passing. But what exactly is behind it? Where does welding begin and where does it end? All this can be explained with the definition of welding.
Table of contents
Estimated reading time: 9 minutes
What is welding and what is it used for?
Welding is a method of joining technology. It is used to join different parts together, particularly in metal construction. This is done by means of a materially bonded connection, which is then inseparable.
Welding creates a material bond between two workpieces. To do this, the two workpieces are heated very strongly at the joint. The material from which the two workpieces are made melts and liquefies slightly. The liquid combines and a microstructure is created. This joint can then no longer be separated. An additional material is usually added to fill the joint.
There are various methods for carrying out welding. The two most important are manual arc welding and gas-shielded arc welding. Gas-shielded welding uses a shielding gas that protects the molten pool and the arc itself from harmful air ingress.
What are the pros and cons of welding?
At first glance, welding is quite simple. There are two workpieces, then a little heat is added and now it's just one workpiece. The connection is secure and durable and there's nothing to complain about.
In reality, however, the whole thing looks a little more complicated. Sure, welding has its advantages. Without these, it would not be used. One of the advantages is that welding can be used to create a wide range of shapes and designs. No additional connecting elements are required. These include screws and bolts, for example. The connection is direct and very strong.
However, these advantages also have disadvantages. Welding is not suitable for all types of materials. Also, only workpieces made of the same material can be welded. Finally, the heat also results in distortion and a change in the structure of the workpieces.
This means that the welding process can only be used for certain joints. But then the advantages outweigh the disadvantages to such an extent that welding has become established in the industry.
How does the welding process work?
There are a number of different welding processes that can be used. These have their own code number in accordance with DIN EN ISO 4063, which standardises them throughout Europe. As already briefly mentioned here, the most important welding processes are manual arc welding and gas-shielded arc welding.
Manual arc welding
In manual arc welding, an electric circuit is used, whereby the arc itself closes this circuit. The circuit exists between a rod electrode and the workpiece. Manual arc welding is considered a simple type of welding and arc welding. This is because the stick electrode performs several functions at the same time.
- Firstly, the electrode supplies the filler metal required to fill the joint.
- Secondly, the electrode supplies the shielding gas for welding. This is bound within the coating of the electrode. As soon as the heat begins to melt the materials, the gas is released.
Welding in this process is usually carried out with direct current. The rod electrode itself represents the negative pole in the circuit. A household socket with 230 V is sufficient as a power source. Alternatively, three-phase current can also be used. In this case, 400 V is required. The three-phase current is then converted into direct current and transformed to the corresponding welding voltage, which is between 15 and 30 V. This means that a low voltage is used to keep the amperage as high as possible.
The arc has a high temperature. This melts the materials and the rod electrode. The devices used today are very compact, making them easy to transport. They are mainly used on construction sites, where they can be used anywhere due to their small size.
Why is manual arc welding complicated?
In the beginning, simple electrodes that were not coated were used for manual arc welding. However, when welding, the welding point must be protected from the air and the associated oxidation, which made this type of welding rather complicated. As a result, coated stick electrodes were soon used. These formed the arc carrier, the filler metal and supplied the shielding gas. This made welding in this process easier.
Today, there are separate electrodes designed for each welding job. Electrode abbreviations are used for this, which are printed on the packaging and provide information about the use for which the electrode is intended. The gases that are released not only serve to shield the electrode from the air. They also stabilise the arc and reduce the burn-off of components within the alloys in the materials. The gases are bound in the coating. When this melts, the gases are released, while the coating itself forms a slag. The slag is lighter than the liquefied steel. This causes it to float and settle on the seam. This results in slower cooling, which in turn reduces the shrinkage stress.
Gas-shielded arc welding
Gas-shielded arc welding is also a variant of arc welding. However, it differs from manual arc welding in that the shielding gases do not come from an electrode. In fact, they are added separately. Their task is to protect the weld pool and the arc from the ingress of air, which is harmful to the welding process.
Two types of gases are used as shielding gases. On the one hand, these are inert gases that do not chemically react with the weld metal. On the other hand, there are active gases such as carbon dioxide, nitrogen and hydrogen. These can react chemically and have an oxidising effect on the weld.
Main process of gas-shielded arc welding
- MIG - Metal inert gas process: An electrode melts and supplies the filler material. Inert noble gases are used as the MIG shielding gas.
- MAG - Metal Active Gas process: An electrode melts and thus supplies the filler material and active gases are used.
- TIG - gas tungsten arc welding: A tungsten electrode is used. This does not melt, so a filler material is supplied separately. An inert noble gas is used as the shielding gas, hence TIG - tungsten inert gas welding.
How are different welding processes structured?
The welding process can be designed in various ways. The main factors here are the weld seam shape and the weld joint. These in turn depend on the thickness of the workpiece, its shape and the welding process itself that is to be used.
The I-seam
The I-seam is a very simple welded joint. This seam is created when two workpieces are welded lying flat next to each other on a straight edge. The seam then extends over the entire height of the edge and slightly overlaps the top of the workpieces on both sides of the edges.
The V-seam
With the V seam, both workpieces are placed next to each other. The edges face each other, but they are slightly angled so that a V is created. The seam then extends across the V and slightly overlaps the edges on both workpieces.
The X-seam
The X-seam is practically a double V-seam. Both workpieces lie next to each other with one edge. However, the edge is angled at the top and bottom so that a double V or X is created in the cross-section. The weld seam then fills both angles, at the top and bottom of the X.
The fillet weld
Here, two workpieces are joined similar to a T. The seam is created at a right angle between the two workpieces.
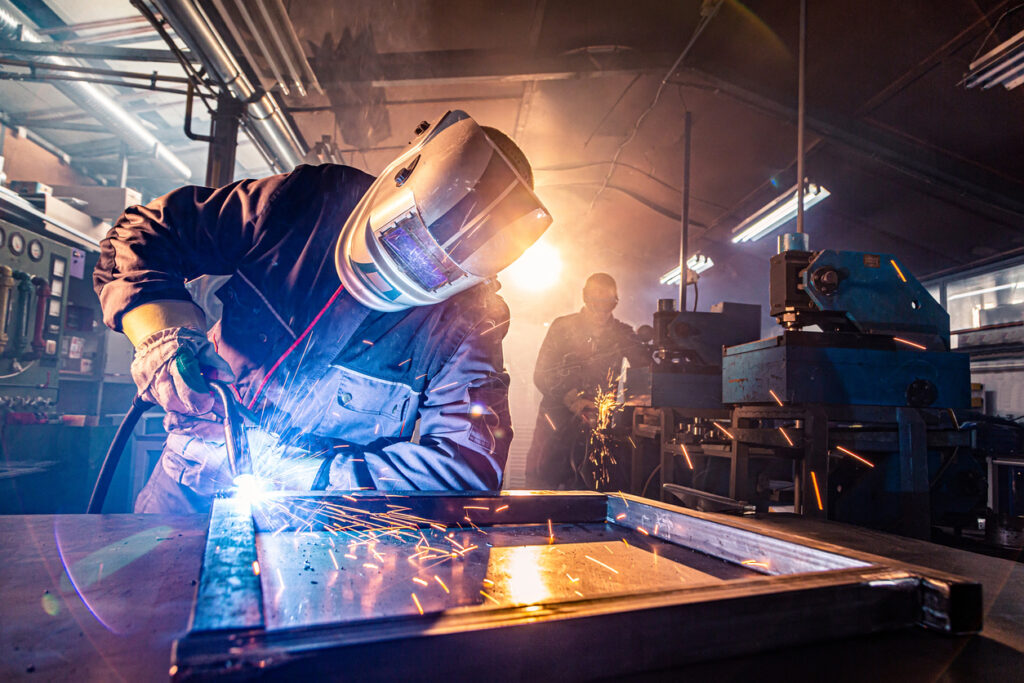
What is a welding joint?
The welding joint depends on the position of the workpieces in relation to each other. The welding joint determines how strong the entire joint that is created will be. This means that the load to which the joint will later be subjected must also be taken into account when selecting the welding joint.
The lap joint
The edges of the two workpieces overlap here. These are then welded on both sides. It is easy to see how the overlap joint is stronger than the butt joint.
The butt joint
With butt joints, the workpieces are positioned opposite each other with a flat edge and are welded straight at this edge.
The T-joint
The T-joint consists of a horizontal workpiece onto which another T-shaped upright workpiece is welded. The weld seam can be placed on one side or on both sides.
The multiple impact
Here, more than two workpieces are joined at different angles in one place. Weld seams are created at all angles between the different workpieces.
Which welding methods are commonly used?
Manual arc welding is very mobile thanks to the compact devices. It is therefore used in pipeline construction, on building sites and in metal construction. It can be used to weld alloyed and unalloyed steels.
MIG-MAG welding is used in the manufacture and repair of motor vehicles. These two processes are also used in mechanical engineering. They can be used to weld alloyed and unalloyed steels as well as aluminium.
The TIG process can be used to weld raw metal and sheet metal. It can also be used for aluminium, titanium, nickel, copper and bronze.
Conclusion
Welding has become an indispensable joining process in today's technology. It joins two workpieces with a material bond and is also inseparable. A filler material is usually used to fill the joint. A shielding gas is also used to protect the weld from the penetration of air. The air would weaken the weld seam by causing oxidation at the joint.
Welds can be categorised according to the shape of the weld seam and the weld joint. The most important welding processes used today are manual arc welding and gas-shielded arc welding. The latter is subdivided into MIG, MAG and TIG.